3Dプリンタにはさまざまな造形方式があり、造形したい製品の形状や用途などによって、適した造形方式が異なります。3Dプリンタの造形方式の中でも、幅広い用途で用いられている造形方式が「光造形方式(液槽光重合方式)」です。
この記事では、同じく代表的な造形方式であるFDM(熱溶解積層方式)との違いや使い分けについて紹介します。
ミクロンオーダーの光造形3Dプリンターは、ぜひ一度BMFまでご相談ください
3DプリンタのFDM(熱溶解積層)方式とは
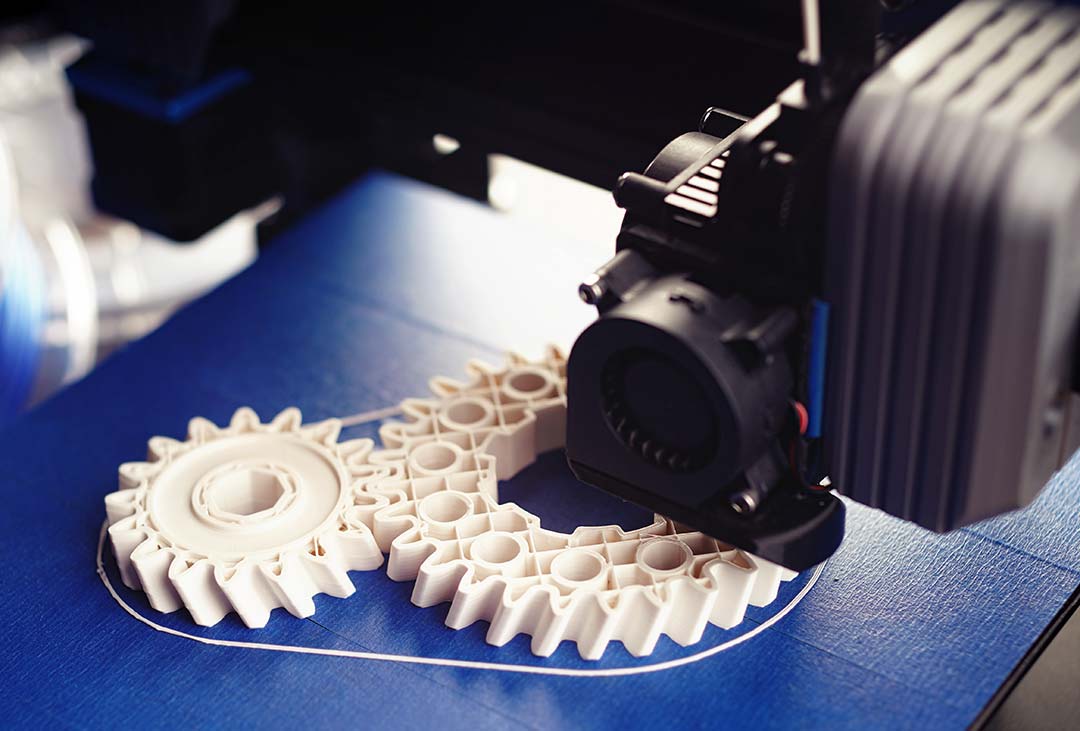
FDM(熱溶解積層方式)は、加熱・溶融した材料を押し出して積層するMEX(材料押出方式)の一種で、主にABS樹脂やPLA樹脂などの熱可塑性樹脂で作られたフィラメントを材料として用います。
FDMでは、最終的な製品の形状を実現するモデル材と、補助となるサポート材の2つの材料が必要です。
狙いの形状を実現できるようにモデル材とサポート材の積層ができたら、サポート材の除去を行います。サポート材の除去方法は導入する設備の種類によって異なり、安価な設備の場合には自動ではなく手作業での除去が必要になるため、注意が必要です。
FDM方式のメリット
FDM方式の3Dプリンタは、家庭用の安価な機種から産業用の高機能な機種まで、幅広い価格帯の製品が販売されています。用途に応じてさまざまな選択肢から選択できる点がFDM方式のメリットのひとつです。また構造がシンプルで小型なので、設置場所に困らないことが多いでしょう。
3Dプリンタの中でも取り扱いが容易であり、市販されている樹脂製品と同様の熱可塑性樹脂を採用できるため、市販品に近い造形物を実現できます。また、あらかじめ材料に着色をしておくことでカラフルな造形が可能です。
FDM方式のデメリット
FDM方式のデメリットとしては、微細な造形が難しい点があげられます。
また、一層ずつ積層する際の積層界面の接着力がそれほど強くないことから、積層界面が脆いといった強度に関する課題もあります。
さらに、積層界面に関しては段差が目立ちやすいというデメリットもあります。
また、造形を行う際の温度管理において一定以上の高温を実現できないことから、材料の選択肢が限られるといったデメリットも考えられます。
サポート材の除去や融点が高いエンジニアリングプラスチックなどの高機能材料を使用したい場合には、高機能なFDM方式の3Dプリンタを採用することで対応可能です。
FDM方式の主な用途
FDM方式の3Dプリンタは、さまざまな用途に採用されています。
例えば、量産品と同様の材料を使用できることから、強度などの機能評価にも対応できる製品の試作品に適用できます。
また、フルカラーの加工にも対応可能なため、着色が必要な製品にも採用可能です。
さらに、簡易的な型や生産工程や開発工程などで用いられる治具、比較的大きなサイズの造形物にも対応できるため、これらの用途で用いられています。
3DプリンタのDLP方式とは
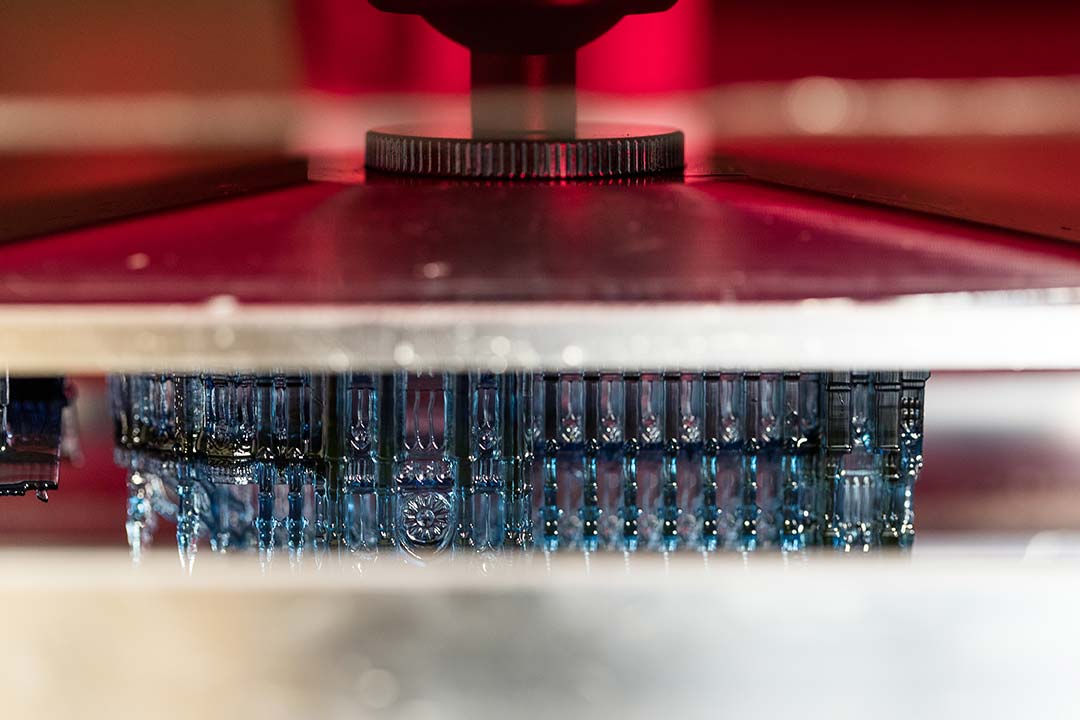
FDM方式と比較される3Dプリンタの造形方式のひとつに、DLP方式があります。
DLP方式は、光造形方式(液槽光重合方式)の一種で、タンクの中に貯めた液状の光硬化性樹脂に対して、プロジェクターなどの光源を用いて、紫外線などを面単位で照射することで材料を硬化させる造形方式です。
光造形方式で採用される光硬化性樹脂には、アクリル樹脂やエポキシ樹脂などがあります。また、ゴムライクやワックスの代用樹脂など、紫外線などを照射して硬化する特徴を持つ、さまざまな樹脂を採用できます。
同じ光造形方式であるSLAではガルバノミラーやレーザーなどを用いますが、DLPではこれらが不要なためSLAよりもコストを抑えて導入することが可能です。
DLP方式のメリット
DLP方式の主なメリットには、造形物の表面を滑らかに造形できる点があげられます。表面が滑らかさ、高い耐久性や塗装性の高さにつながっています。
また、サポート材を用いることで複雑な形状の造形物や大型の造形物にも対応可能です。デザイン面では、透明な光硬化性樹脂を採用することで、内部を確認できる透明な造形物を作成できます。
3Dプリンタは、射出成形などの加工法と比較して生産性が高くありません。しかし、DLPは光を広範囲に照射することで一度の複数の製品を造形できるため、3Dプリンタの加工の中では高い生産性が期待できます。
DLP方式のデメリット
DLP方式にはメリットが多いですが、採用する際にはデメリットが許容できるかどうかも確認する必要があります。
DLP方式のデメリットとして課題になるのが、耐候性の低さです。一般的に、光硬化性樹脂は耐候性が低いことで知られています。屋外や窓際などの紫外線の影響を受けやすい環境で使用すると、強度に問題が出るため注意が必要です。
また、サポート材を用いるため、サポート材の除去が必要です。エタノールなどの洗浄液で洗浄を行いますが、適切な処理をしないと造形物に影響が出てしまいます。また、保管時にも紫外線の影響を受けないように適切に管理する必要があります。
DLP方式の主な用途
DLP方式では、その特徴を活かして幅広い用途に使われています。
例えば、透明な材料で造形できることから、内部の状態を確認する必要がある工業製品の試作品に活用できます。また、DLP方式の高性能な3Dプリンタを採用すれば、歯科医療や半導体製造装置向けの微細で複雑な形状の製品にも適用可能です。
さらに、生産性が高いことから量産が必要な製品への適用や複雑で高精度の造形が必要なフィギュア、教育用途に採用されることもあります。
FDM方式とDLP方式の比較
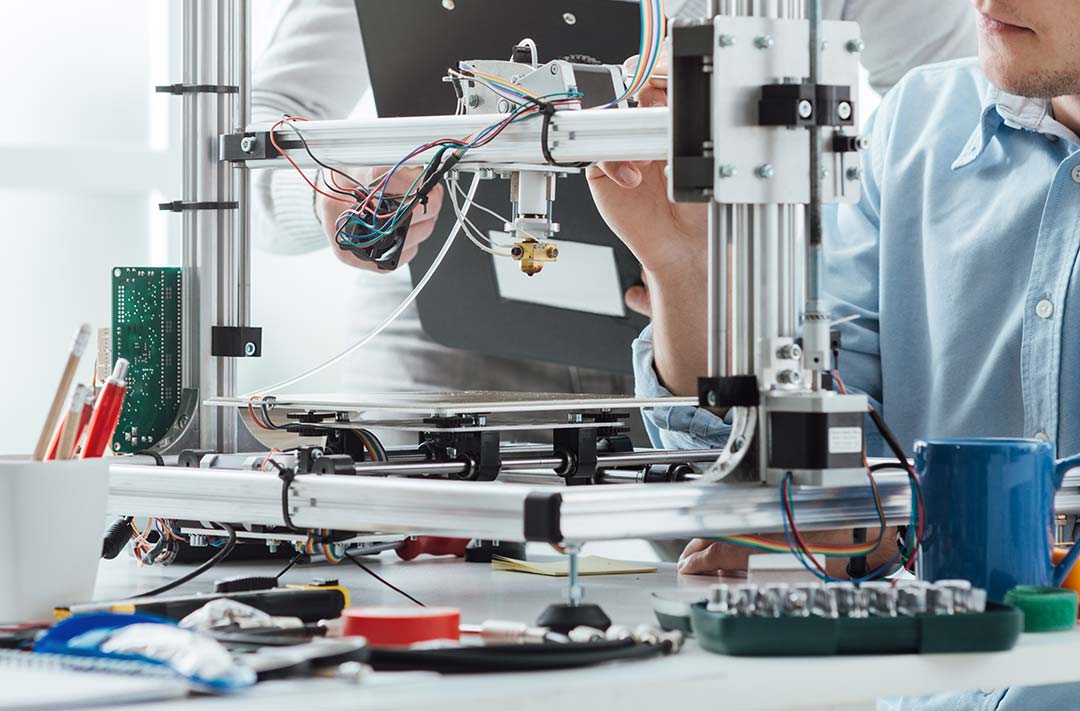
FDM方式とDLP方式の使い分けを考える場合、どのような観点で比較すればよいのでしょうか。
FDM方式は熱可塑性樹脂を採用し、最終製品と同等の強度や特性を再現できるため、最終製品の機能確認を行う試作品への適用が効果的です。また、カラー材料を使用できることから、多様なカラーバリエーションが必要な場合にも適用できるでしょう。
一方で、DLPでは造形速度が速く高精度の造形が可能なことから、量産製品などのように一定以上の生産性が必要な製品。また、複雑な形状で高い造形精度が求められる製品への適用が望ましいでしょう。
BMF独自の光造形(DLP)方式のアプリケーション
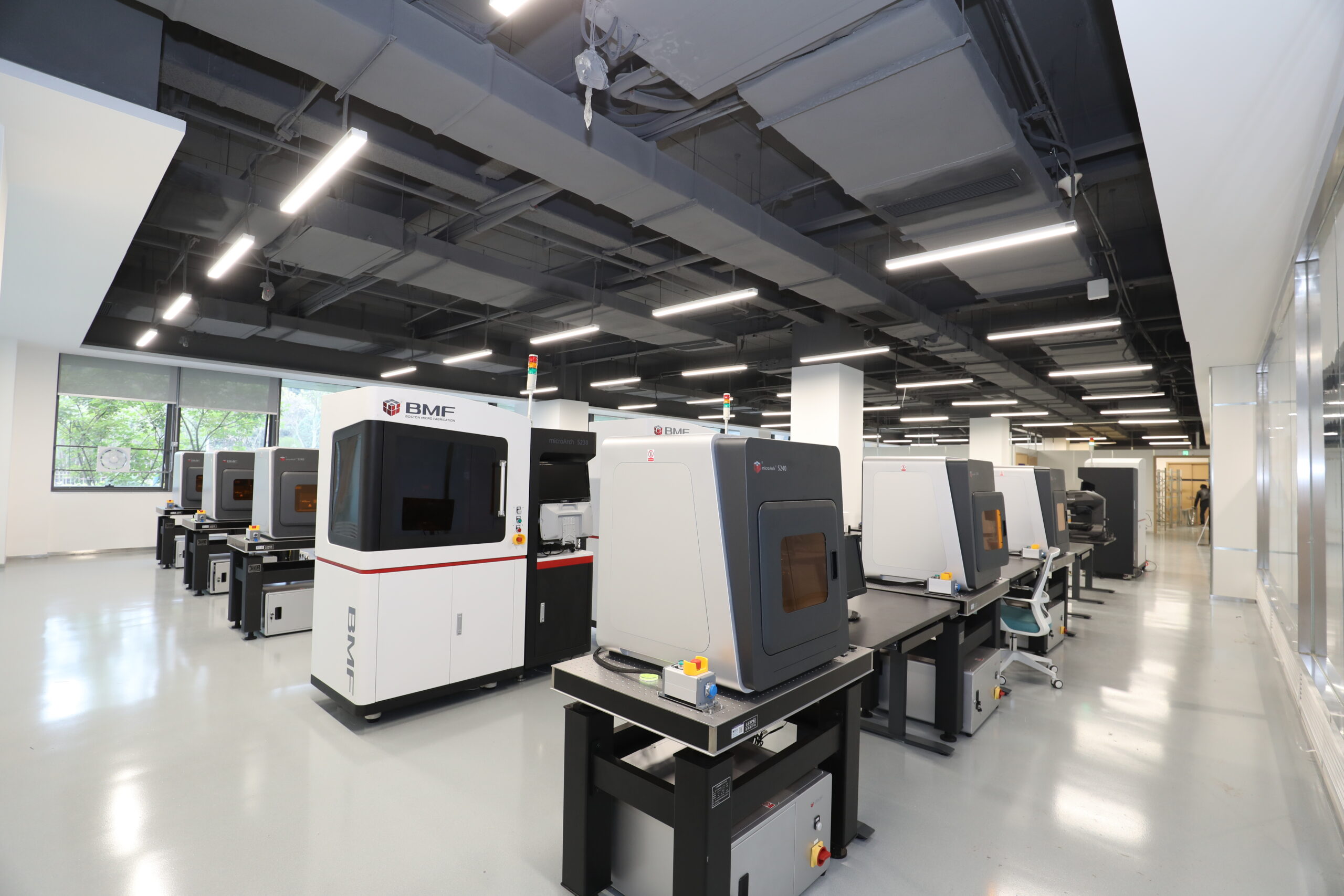
BMFでは高い造形精度が求められるなか、PµSL(Projection Micro-Stereolithography)と呼ばれる、独自の光造形技術を開発。PµSL技術は、高い精度が求められる産業用途のニーズに応えています。
BMFの超高解像度3Dプリンタによる、アプリケーションをご紹介します。
電子部品
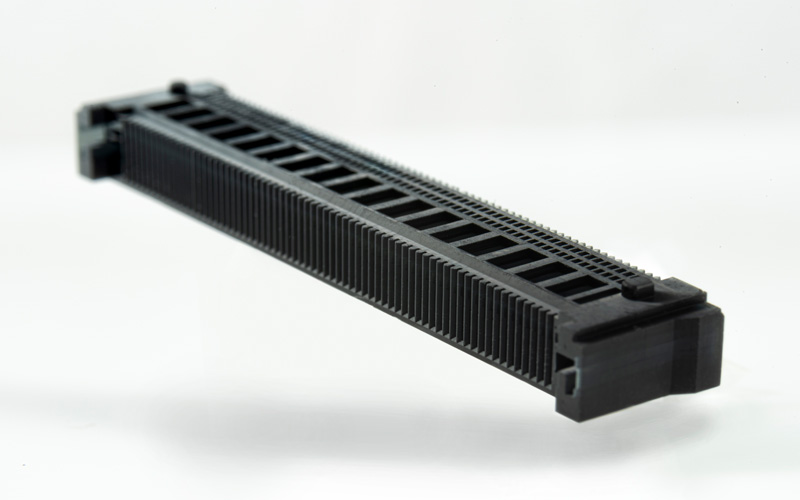
電子部品の試作では、複雑な形状で微細な加工を必要とする部品を、高精度に加工する必要があります。また、製品開発期間を短縮するために短納期での試作が必要である一方で、大量生産は不要です。
PµSL技術は、大手電機部品メーカーのコネクタや、ソケットなどの精密部品の試作開発でも採用されています。
医療業界
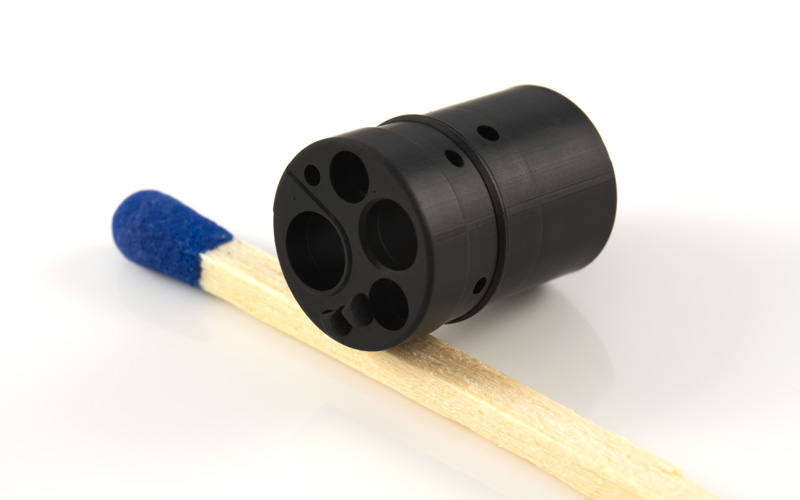
患者ごとにオーダーメイドが必要な部品や、複雑な加工が必要な医療部品の中には、射出成形や切削加工では対応が難しい場合があります。このような部品の製造には、3Dプリンタが最適です。
PµSL技術を使用して、体内に埋め込むステントや医療チューブ、内視鏡ハウジング、遺伝子シーケンサーバルブプレートなど、医療部品の試作開発が進んでいます。
研究機関

大学や研究機関では、マイクロメカニクスの研究や新素材の開発など、新技術の開発に使われています。
PµSL技術は、バイオニクス、マイクロ流体デバイス、マイクロロボット、マイクロシステムなど、さまざまな分野の基礎研究に利用されています。
光造形3DプリンタとFDMとの違いは?まとめ
3Dプリンタの造形方式の中でも生産性が高く、精度の高い造形を実現できる光造形方式は、量産用途や複雑・微細な形状、滑らかな表面の製品を製造する際に適した造形方式です。
実際の製品と近い材料で機能確認もできる製品の造形が可能である一方で、表面の滑らかさなどで光造形方式に劣るFDM方式とは異なる特徴を持つため、用途に応じて使い分けるといいでしょう。