セラミックは、高い強度や電気絶縁性などの優れた特性を持つ材料で、幅広い製品への採用が期待されています。一方で、セラミックは加工が難しいことでも知られ、近年では3Dプリンターによる造形のニーズが急速に増加しています。
この記事では、セラミックにおける3D造形のニーズと3Dプリンターの活用例について解説します。
ミクロンオーダーの光造形3Dプリンターは、ぜひ一度BMFまでご相談ください
セラミックの特徴
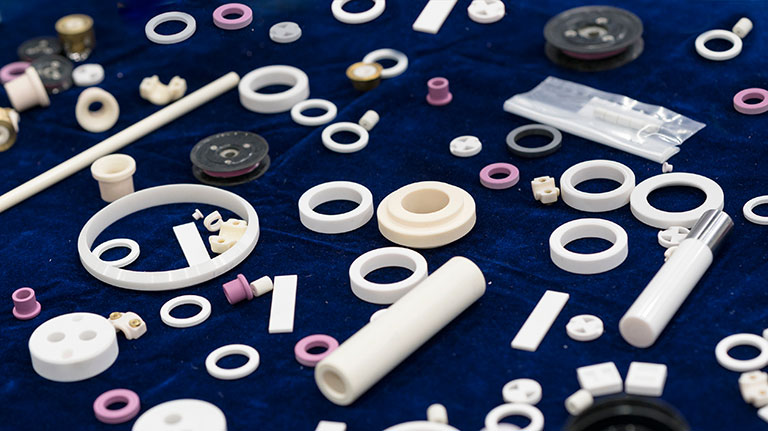
セラミックは広義では、固体材料の中でも金属や有機材料以外の「無機材料」のことを指します。
セラミックに分類される代表的なものには、非金属の元素である「シリコン」や「ダイヤモンド」、金属元素と非金属元素が組み合わさって構成されている「無機化合物」があげられます。
セラミックにはさまざまな材料の組み合わせがあるため、その特性も多岐にわたります。陶磁器やガラス、セメントなどからイメージされるように、耐熱性や耐食性、電気絶縁性などの特徴を持った材料です。
セラミックの中でも、特に優れた特性を持つ材料を「高機能セラミックス(ファインセラミックス)」とよび、自動車や半導体を中心に、産業機械や医療などの分野で必要不可欠な材料となっています。
セラミックにおける3D造形のニーズ
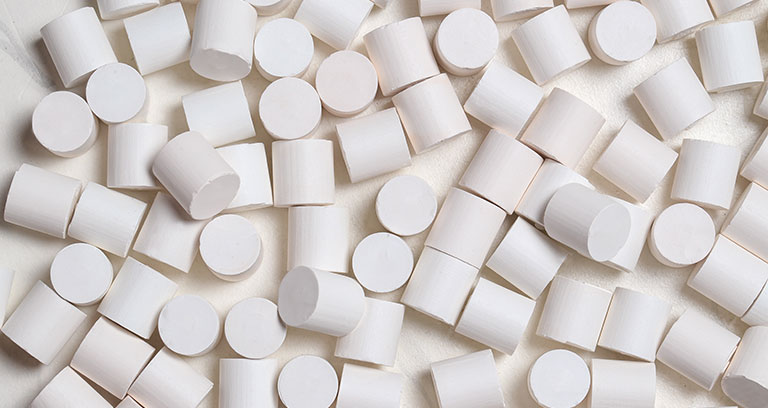
セラミックの加工では、「切削加工」「放電加工」「レーザー加工」「射出成形」など、さまざまな加工法が用いられます。しかし、特性が多岐にわたるセラミックは、どの加工法においても材料の特性に合わせた条件の設定が難しいことが課題です。
また、セラミックは硬く脆い脆弱材で、切削加工時には欠けやワレが生じる難削材として知られています。射出成形においては、材料となるセラミック粉末を適切に管理するのが難しく、材料の保管に多大なコストがかかってしまう点がデメリットです。
このような課題を解決するセラミックの加工法として、「3D造形」に注目が集まっています。3Dプリンターを用いた3D造形では、切削加工や射出成形では難しい形状を造形することができます。
また、射出成形の場合に必要となる金型が不要なため、製造期間とコストを削減できる点が、3D造形の大きなメリットです。
セラミック3Dプリンターの造形種類
セラミック材料に対応した3Dプリンターに採用されている造形方式は、主に以下の3種類です。
光造形法(セラミック3D造形)
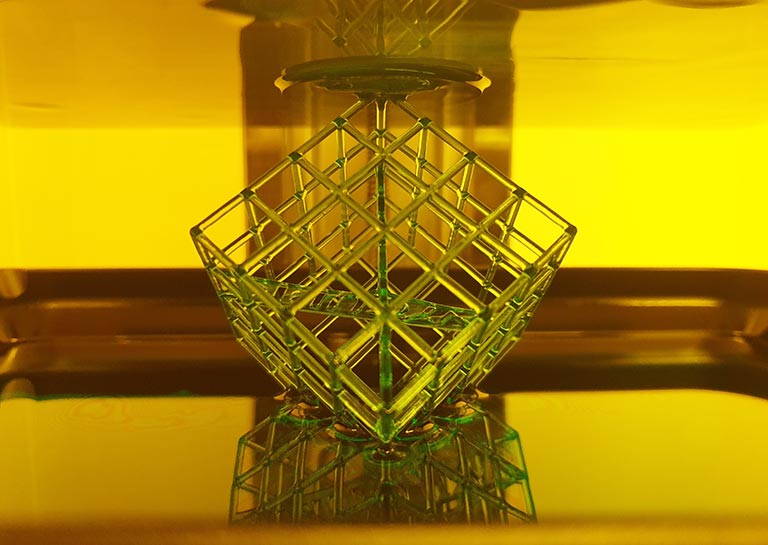
光造形法は3D造形における代表的な造形法のひとつで、主に光硬化性樹脂が材料として用いられます。
造形ステージに積層させた材料に紫外線レーザーを照射し、一層ずつ硬化させていくことで、精度が高く滑らかな表面の造形が可能です。
近年は、樹脂とセラミックを配合した「セラミック樹脂」を光造形法の材料として使用することもあり、造形後に高温の窯で焼成することで、製品が完成します。
粉末状のセラミックをレーザー焼結する場合に比べて、高い強度と耐熱性を持つ点が大きな特徴で、航空宇宙産業や電子デバイスの材料としての採用が期待されています。
レーザー溶融法(セラミック3D造形)
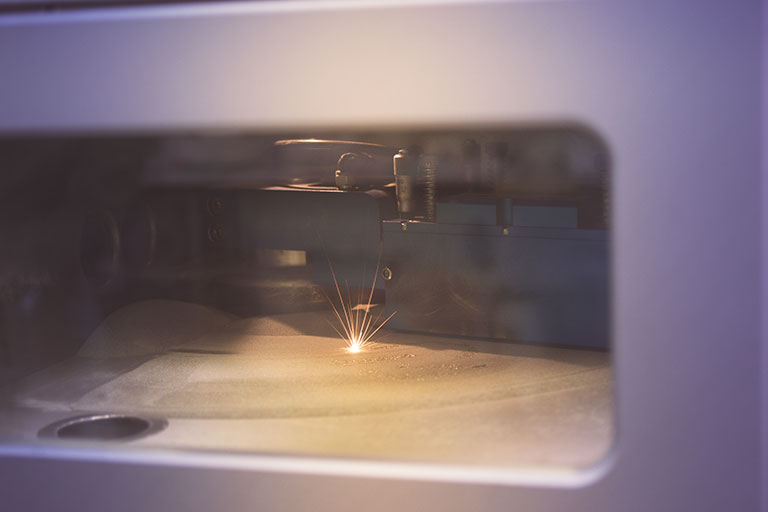
レーザー溶融法は、粉末状の材料に対してレーザーを照射することで造形する方法です。金属材料を用いることが一般的ですが、焼結が必要なセラミックの加工にも適しています。
細いレーザーを照射することで、精密な形状の部品を短期間で製作することが可能です。例えば多孔構造や格子構造を埋め込んだ中空形状など、他の加工法では実現できないような形状に対応しています。
焼結時に微小な隙間が生まれることで強度に課題がありましたが、焼結後に隙間を埋めるような加工法が開発されており、複雑な形状でも高機能セラミックス同等の強度を実現しています。
押出法(セラミック3D造形)
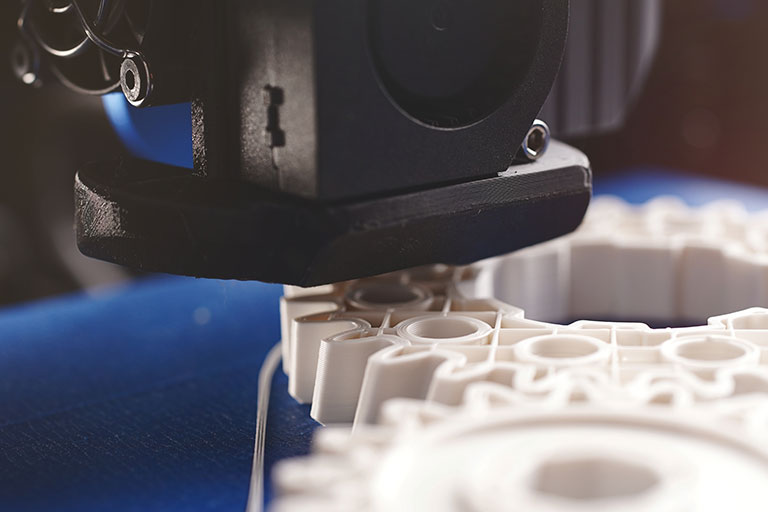
押出法は、加熱し溶融した材料を造形ステージに押し出していくことで、狙いの形状を実現する加工法です。
セラミック材料を押出法で加工する際には、あらかじめセラミックの粉末をバインダーとなる樹脂と混錬し、加熱溶融させます。ノズルから、狙いの形状になるように一層ずつ射出し、冷却することで固化させる工程を繰り返し行うことで、狙いの形状を実現できます。
固化した材料は、脱脂・焼結することでセラミックの焼結部品として完成しますが、レーザー溶融法と同様に微小な隙間が生まれてしまうため、強度を確保するための工夫が必要です。
産業分野でのセラミック3Dプリンターの活用について
小ロットで複雑な形状のセラミック製品を実現できる「セラミック3Dプリンター」は、さまざまな産業分野で活用が進んでいます。
自動車産業
ファインセラミックスは高い強度と耐熱性を持っているため、耐熱性が重視されるエンジン部品への適用が期待されています。また金属よりも軽くできるため、自動車の軽量化への活用も可能です。
特に現在は、環境面の規制が厳しくなっており、排ガス規制や燃費・電費に優れた車両の需要が高まっています。
航空宇宙産業
航空機やロケットは、機体表面と大気の摩擦で高温にさらされるため、耐熱性と耐摩耗性が必要とされ、ファインセラミックスの活用が期待できます。
ボディだけでなく、ロケットのジェットエンジンやノズル部品なども耐熱性が要求されるため、セラミックの特徴をいかせるでしょう。
また、小惑星探査機の「はやぶさ」や「はやぶさ2」では、高い強度や耐食性、耐熱性、絶縁性が要求されるリチウムイオン電池の端子部にセラミック部品が採用されました。すでにさまざまな部品向けに、セラミック部品の採用が進んでいます。
電子部品
自動車の電動化やIoTの普及に伴い、電子部品の小型化・高速化が求められており、その実現にはファインセラミックスが欠かせません。
高性能な電子部品を実現するためには、複雑な形状に加工する必要がありますが、3D造形であれば他の加工法では造形できないような、中空構造などの複雑な形状も実現できます。
高性能・高機能な新製品の開発が期待できるセラミックの3D造形は、今後高性能化が期待される電子部品の領域において、必要不可欠な技術です。
医療分野
セラミックは、樹脂や金属などと比較して生体適合性が高いため、人工骨や歯科用インプラントをはじめ、医療器具や再生医療用部品などへの活用が期待されています。
特に、人工骨や歯科用インプラントなどは、患者一人ひとりに合わせて形状を調整する必要があり、一点ものとなってしまう可能性が高く、3D造形であればコストと期間を抑えることが可能です。
セラミックによる3Dプリンタの活用事例
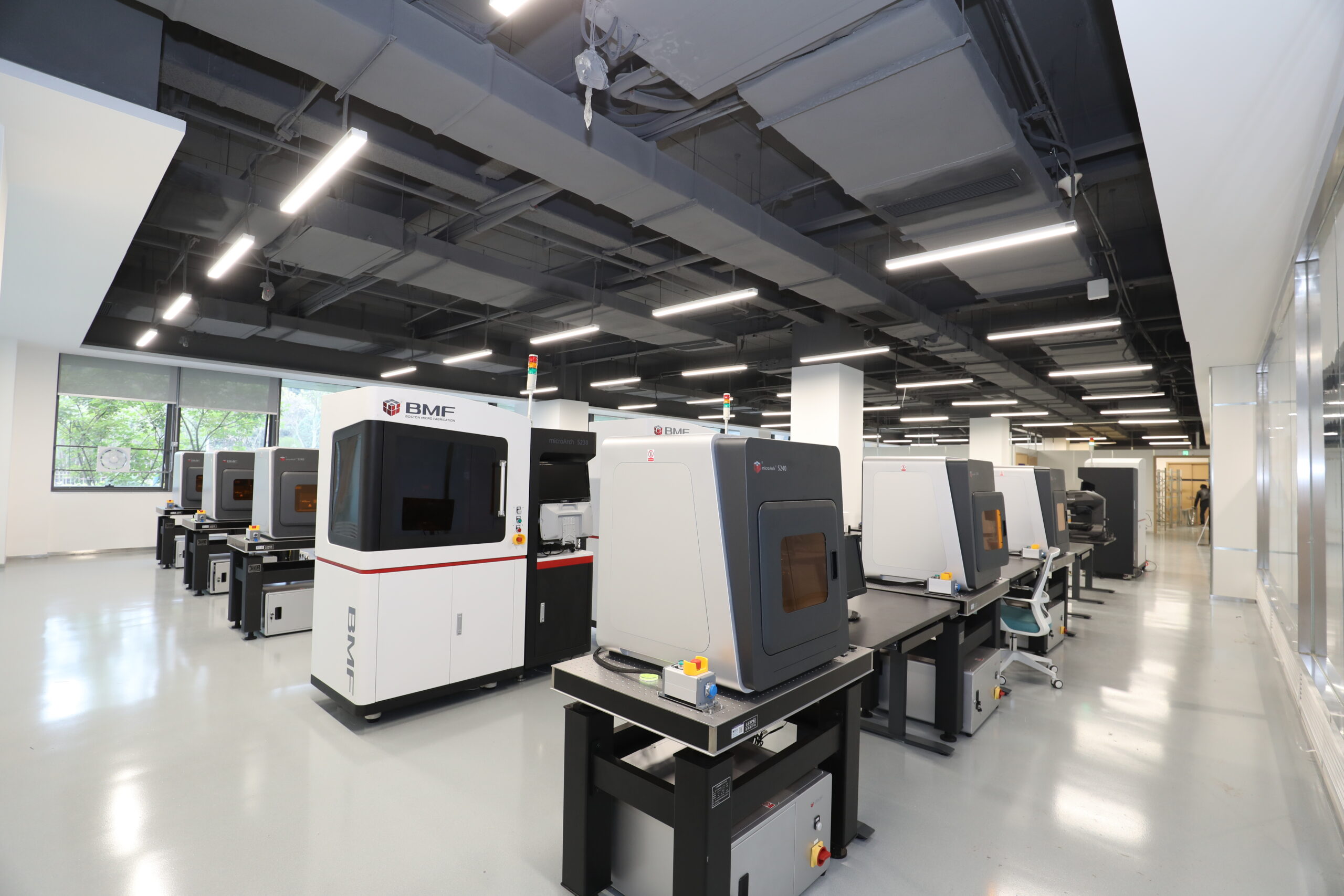
BMFでは高い造形精度が求められるなか、PµSL(Projection Micro-Stereolithography)と呼ばれる、独自の光造形技術を開発。樹脂だけでなく、アルミナセラミックスの試作を提供しています。
PµSL技術による、セラミックによる3D造形の事例をご紹介します。
セラミック医療部品
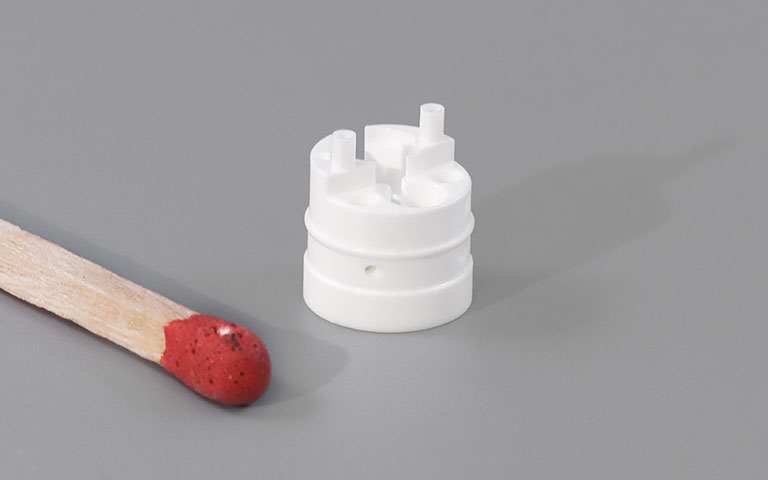
セラミックは、生体適合性に優れているため、インプラントや人工関節をはじめ、内視鏡ハウジングや心臓血管ステント、シリンジニードル(注射針)など、さまざまな医療部品に適用されています。
セラミック機械部品
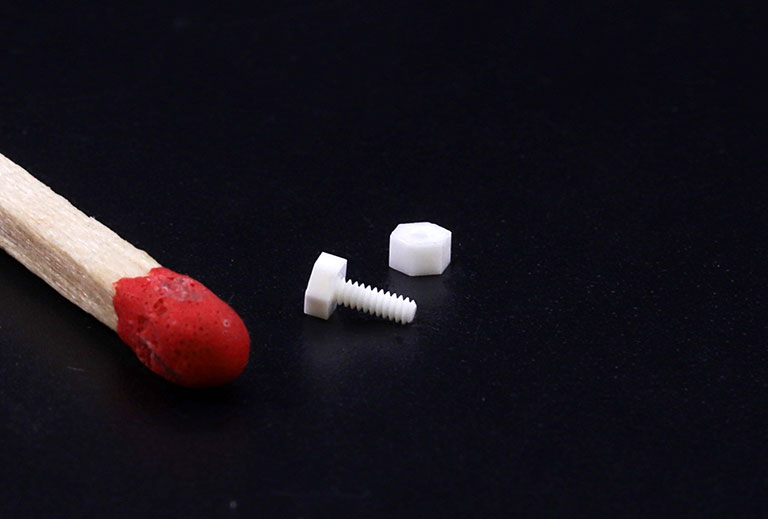
精密ネジ(雄ネジ・雌ネジ)部品の事例です。 セラミックは、電気絶縁性、耐摩耗性、耐熱性に優れているため、半導体製造や電子部品の製品開発など、さまざまな分野での活用が期待できます。
PµSL技術では、ネジ径2.4mmの精密ネジを2ミクロンの光学解像度で造形することが可能です。
セラミック構造部品
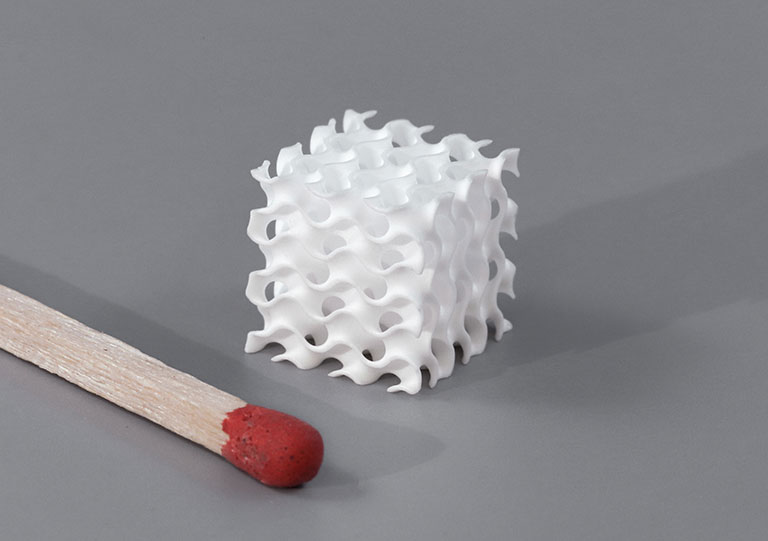
ジャイロイド(周期的なパターンが複雑に入り組んだ構造体)などの構造部品の事例です。
耐薬品性、耐酸性・耐アルカリ性に優れたセラミックで造形することで、研究機関や化学分野での応用が期待されています。
PµSL技術では、壁厚さ僅か0.22mmの構造体を10ミクロンの光学解像度で造形することが可能です。
セラミックにおける3D造形のニーズまとめ
高い強度や電気絶縁性などの特性を持つセラミックは、加工が難しい材料としても知られています。3Dプリンタであれば、セラミックの脆弱性の影響を受けず、金型なども必要としない上に、複雑な形状も実現可能です。
今後、自動車や航空宇宙産業、医療分野など、さまざまな領域で需要が増えるセラミックの特徴を十分にいかすためには、3Dプリンタでの造形が必要不可欠になるでしょう。