創薬やヘルスケア、また工業や医療用途でもマイクロ流体の特性を利用したマイクロ流体デバイスの活用が進められています。マイクロ流体デバイスの材料にはさまざまなものが使われており、その中でもPDMSを用いたマイクロ流体デバイスが「PDMSデバイス」です。
この記事では、材料としてのPDMSやPDMSデバイスの特徴、またPDMSデバイスの用途や製作方法であるフォトリソグラフィなどについて紹介します。
ミクロンオーダーの光造形3Dプリンターは、ぜひ一度BMFまでご相談ください
PDMSとは?
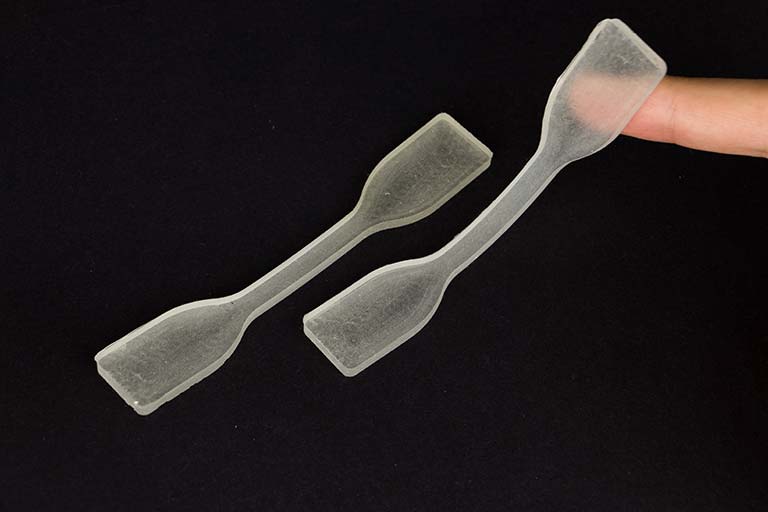
PDMS(ポリジメチルシロキサン)はシリコンの一種で、透明であり不活性、非毒性、不燃性といった特徴を持ちます。また、表面張力を低下させる特殊な流動特性を持つことから、その特性を活かしてさまざまな製品に採用されています。例えば、コンタクトレンズや消包剤、シャンプーなどに加えて、コーキングや潤滑剤、耐熱タイルなど、その用途はさまざまです。特に、マイクロ流体デバイスの素材としては長い間採用され続けており、工学的に重要な材料のひとつです。
PDMSがマイクロ流体デバイスの材料に採用される理由として、上記で紹介した特性に加えて、PDMSが高い弾性を持ち加工しやすいことがあげられます。これらの特性が微細な流路構造に適していることから、マイクロ流体デバイスに採用されています。
一方で、強度がそれほど高くないことから使われ方が限定されること、また成形方法によっては品質が安定せず、複雑な形状の実現が難しいことがデメリットです。成形方法については、3Dプリンタの活用により解消されつつあります。
PDMSデバイス(PDMSチップ)の特徴
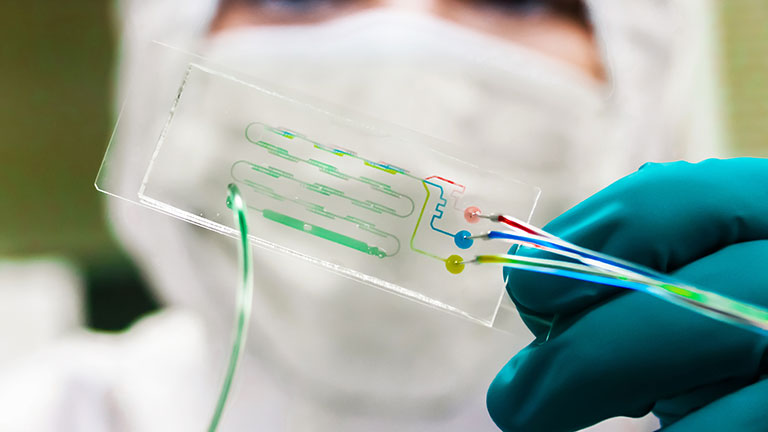
PDMSデバイスとは、PDMSを材料としたマイクロ流体デバイスを意味する用語で、PDMSチップと表現されることもあります。
そもそもマイクロ流体デバイスとは、マイクロ流体力学が適用できる微小な経路を基板に形成した装置で、ガラスや樹脂、PDMSなどのシリコンが材料として使用されます。マイクロ流体力学で重要な「層流」が形成されるため、流体の挙動が予測しやすいという特長を活かしてさまざまな試験に活用されているデバイスです。
例えば、化学反応を均一に行いたい場合や温度変化を均一に保ちたい場合には、マイクロ流体デバイスの利用が効果的です。また、希少な試薬や高額な試薬を使用する場合に、マイクロ流体デバイスであれば必要な試薬が少量で済む点も大きなメリットとなります。
PDMSデバイスは、ガラスや樹脂を用いたマイクロ流体デバイスと比較して以下で紹介するような特徴を持ちます。材質によって特徴が異なるため、マイクロ流体デバイスの用途に合わせて材質を選定することが重要です。
形状の自由度が高い
PDMSデバイスは、フォトリソグラフィやカッティングプロッタなどにより製作することが可能です。また、近年は、高精度で加工することが可能な3Dプリンタが開発されていることから、PDMSデバイスの製作方法として、3Dプリンタの採用も進んでいます。
近年開発が進められている3Dプリンタは、形状の自由度が高く金型などが不要で短時間で加工できることから、細かい形状の調整をしながら試験を行うことが可能です。そこで、3DプリンタによるPDMSデバイスを試作目的で活用する機会が増えています。
製作時間が短い
3Dプリンタを使用してPDMSデバイスを製作することは、ガラスを用いたマイクロ流体デバイスと比較すると短期間で製作することが可能です。製作したい形状の3Dモデルを準備していれば、数時間で製作できるでしょう。
一方で、大量生産が必要な場合には、樹脂を利用して射出成形を行う方が望ましい場合があります。金型の製作期間や後加工が必要といったデメリットもありますが、数量が多い場合には射出成形の採用を検討する必要があります。
コストを抑えられる
3Dプリンタを用いたPDMSデバイスは、初期コストや製作コストを抑えてデバイスを製作することが可能です。PDMSは、材料としてのコストが低いです。
射出成形でマイクロ流体デバイスを製作する場合には、金型が必要なため初期コストや近年課題になる金型の保管コストが大きくかかります。大量生産する場合には問題ありませんが、製作数量がそれほど多くない場合には、1つあたりのコストに大きな影響が生じます。
3DプリンタでPDMSデバイスを製作する場合には、金型は不要であり金型製作費用や金型保管費用などが不要なため、コストを抑えることが可能です。
耐薬品性が低い
紹介したように、PDMSデバイスにはさまざまなメリットがありますが、デメリットもあります。例えば、ガラスなどの耐薬品性が高い材料と比較して耐薬品性が低いこと。また、疎水性が高いことがあげられます。
マイクロ流体デバイスで扱いたい試薬の種類によっては対応していない場合があるため、PDMSデバイスを使用しても問題ないかはあらかじめ確認しておくことが重要です。
PDMSデバイス(PDMSチップ)の用途
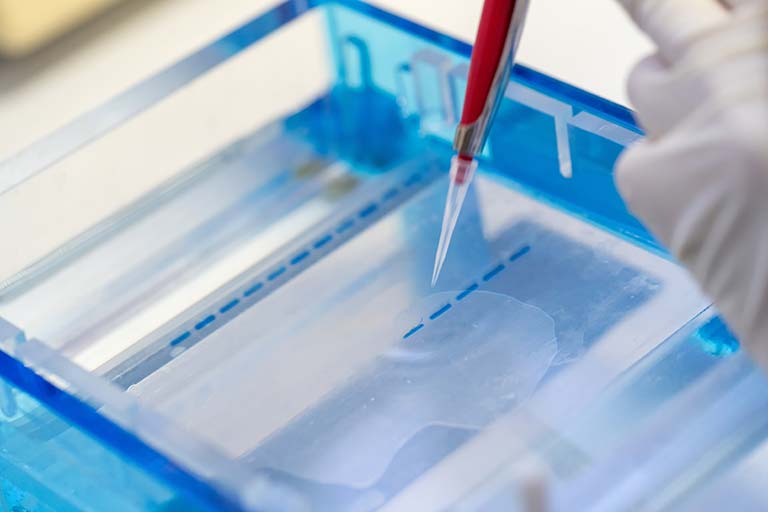
PDMSデバイスは、その特徴を活かしてさまざまな用途で用いられています。
例えば、光透過性を持つことから、マイクロ流体デバイスを使用した材料の分析や化学変化を行う際の状態観察などが可能です。また、PDMSの高い弾性を活かして、遺伝子解析などを含む医療用途にも使用される機会が増えています。
他にも、層流を生じさせることが可能なマイクロ流体デバイスの特徴を活かして、創薬や微小量の化学合成など、さまざまな用途に採用されています。
フォトリソグラフィによる製作方法について
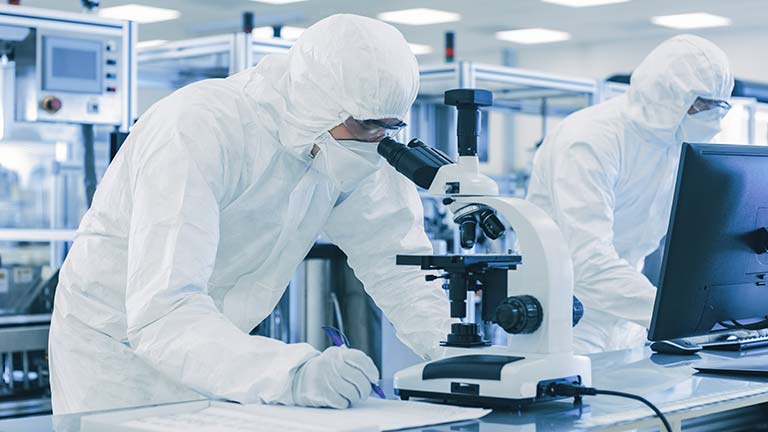
PDMSデバイスは主に、フォトリソグラフィによって製作されます。
フォトリソグラフィとは、基板上に精密にパターン化された薄膜を形成する微細加工技術です。フォトリソグラフィによって形成された薄膜によって、マイクロ流体デバイスの微細な流路を実現します。
フォトリソグラフィは、加工精度が高いことからマイクロ流体デバイス以外にも半導体関連などの精密加工に採用される加工方法です。また、加工時間が短く低コストでパターンを形成できることから、PDMS以外にもさまざまな材料に採用されています。
一方で、フォトリソグラフィは平坦な基板にしか適用できないため、3次元に複雑な形状の実現は困難です。また、空気中の微粒子や化学汚染物質などの影響を受けることから、クリーンルームなどの管理された状況でしか使用することができません。
BMFにおけるPDMSデバイスのアプリケーション
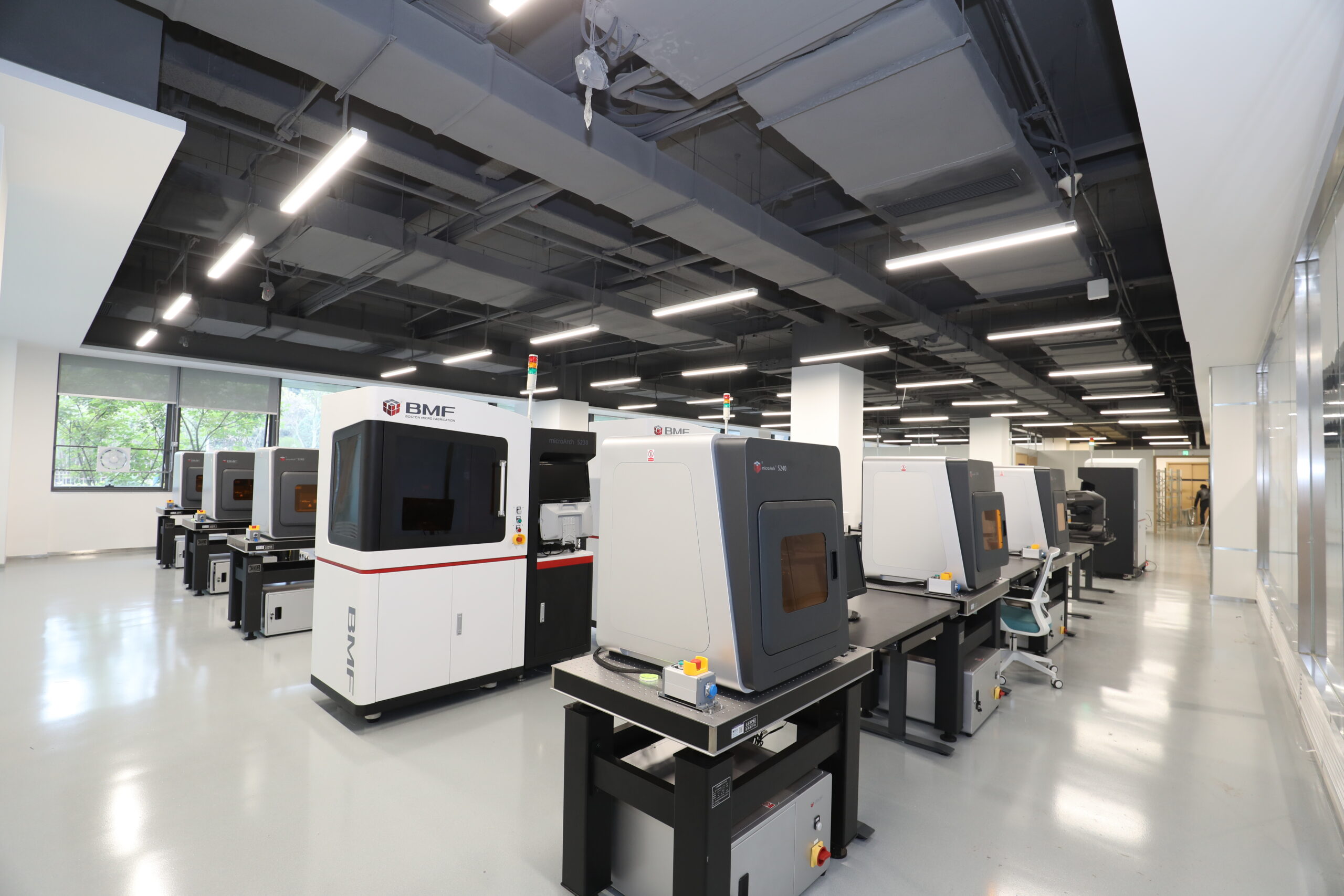
BMFではPµSL(Projection Micro-Stereolithography)と呼ばれる、独自の光造形技術を開発。ミクロンオーダーの造形精度で、高い精度が求められる産業用途のニーズに応えています。
BMFでは、新たにPDMSデバイスのモールド印刷に適した「可溶性犠牲樹脂」を開発しました。
可溶性犠牲樹脂は、硬化後に熱アルカリで溶解することができ、切削加工や射出成形が苦手とする複雑な形状の造形について、さらに精密で高速な造形を可能にします。
犠牲樹脂とPDMSキャスティングプロセス
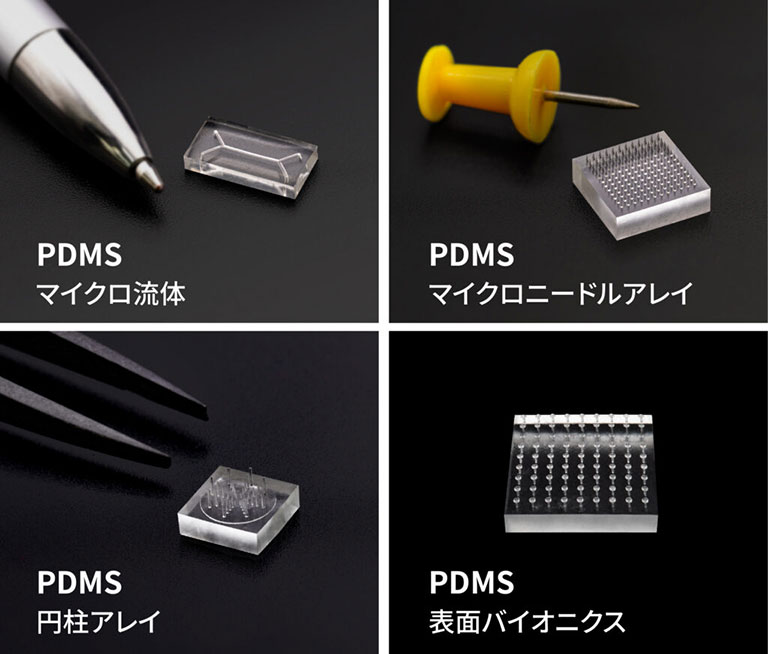
可溶性犠牲樹脂で印刷したマスターモールドでPDMSを成形し、その後マスターモールドを熱アルカリで溶解することで、精密で複雑な三次元微細構造を持つPDMSデバイスを簡単に製作することができます。可溶性犠牲樹脂は 射出成形用のモールド印刷などにもその用途が広がっています。
PDMSデバイスとはまとめ
低コストで透明、特徴的な流動特性を持つPDMSを用いたPDMSデバイスは、マイクロ流体デバイスの中でも幅広い用途に採用されています。ガラスやPDMS以外の樹脂と比較してさまざまなメリットがあるため、今後も用途が広がっていくでしょう。
この背景には、フォトリソグラフィや3Dプリンタなど製作方法に関する技術開発が大きく寄与しています。特に、高精度な3Dプリンタの開発によって複雑な形状も実現しやすくなるため、今後はさらにPDMSデバイスの活用が進められるでしょう。