製造業で活用が進められている3Dプリンタは、さまざまな造形方式が開発されており、それぞれ対応している材料や造形物の特徴が異なります。3Dプリンタを導入しても、造形方式の違いにより、目的の造形物を製造できない場合があるため注意する必要があります。
この記事では、3Dプリンタの基礎知識として、代表的な造形方式の特徴を紹介します。自社の目的にあった3Dプリンタの選定に活用いただければ幸いです。
ミクロンオーダーの光造形3Dプリンターは、ぜひ一度BMFまでご相談ください
3Dプリンタの造形方式と特徴の比較
3Dプリンタにはさまざまな造形方式があり、それぞれ適用できる材料や特徴が大きく異なります。3Dプリンタで目的とする製品・試作品などを実現するためには、あらかじめ3Dプリンタの造形方式とそれぞれの特徴を把握しておくことが重要です。
ここでは、代表的な造形方式を7種類に分類し、それぞれの造形方式の特徴を紹介します。
光造形方式
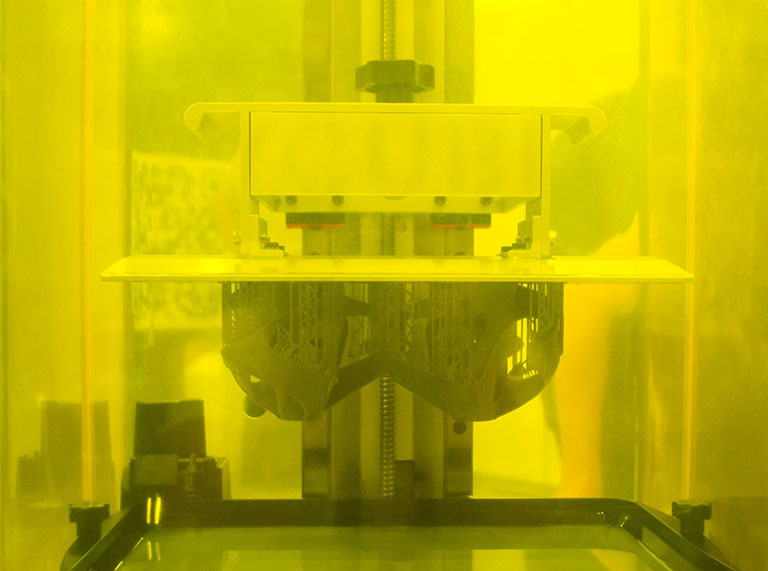
光造形方式は、液槽光重合方式ともよばれ、液体状の光硬化性樹脂をタンクに貯めた状態で、造形物の形状に合わせてレーザーや紫外線などを照射することで硬化させる造形方式です。
なめらかな表面の造形物を実現できることに加えて、光の照射範囲を工夫することで複数の製品を同時に造形できるため、3Dプリンタの中では生産性が高い点も特徴のひとつです。
一方で、光硬化性樹脂は強度や耐候性が低いため使用環境に注意が必要であり、造形後に洗浄が必要な点や洗浄溶液の取り扱いに注意が必要な点はデメリットといえます。
FDM方式
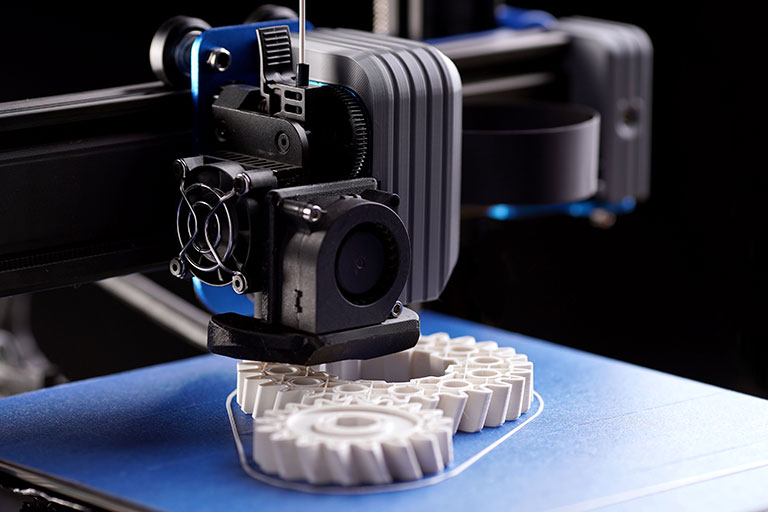
FDM方式は、3Dプリンタの造形方式の中でもっとも代表的で、熱溶解積層方式ともよばれます。材料となる熱可塑性樹脂を熱源によって加熱・溶融し、3Dプリンタのノズルから押し出しながら積層し狙いの形状を実現する造形方式です。
FDM方式の材料として用いられる熱可塑性樹脂は、樹脂加工の代表的な加工法である射出成形でも用いられます。FDM方式ではエンジニアリングプラスチックなどの高性能な材料を含め、さまざまな材料を使用できます。
射出成形などの量産品を製造する際の加工法で用いられる材料を使用できるため、FDM方式で製造した試作品は量産品と同等の性能試験が可能です。
一方で、FDM方式は造形する際の層ごとの段差が目立ちやすい点や精度がそれほど高くないといったデメリットがあります。高い精度やデザイン性が必要な場合には、他の造形方式も検討するといいでしょう。
インクジェット方式(材料噴射方式)
後述するバインダージェット方式も含めてインクジェット方式として表現することもありますが、ここでは主に造形に用いる材料を噴射する造形方式をインクジェット方式とします。
インクジェット方式は、3Dプリンタのノズルから造形物の材料と造形をサポートする材料をステージに噴射し、使用する材料に適した硬化方法で積層させていく造形方式です。
インクジェット方式では、紫外線によって硬化する光硬化性樹脂や冷却によって硬化する金属など、さまざまな材料に対応しています。また、溶融した材料に着色剤などの添加剤を混ぜることで、フルカラーの造形が可能であり、造形精度が高い点もメリットのひとつです。
一方で、特に光硬化性樹脂などを使用する場合には強度や耐候性に課題があるため造形物の用途が限られます。また、3Dプリンタの中でも造形速度を速くすることが難しいこと、サポート材が必要なことから、生産性や生産コストに関しては注意が必要です。
バインダージェット方式
バインダージェット方式は、材料噴射方式と同様にインクジェット方式に分類されることがあります。材料噴射方式では、造形材料とサポート材をインクジェット方式で噴射しますが、バインダージェット方式で噴射するのは、材料を硬化させる際に必要な結合剤です。
粉末状の材料を敷き詰め、造形したい部分に対してバインダーを噴射し、材料とバインダーの熱反応や化学反応を引き起こすことで、材料を固化します。材料は粉末であればいいため、樹脂や金属などの代表的な材料だけでなく、砂や石膏なども利用可能です。
適用できる材料の種類が多いことに加えて、造形材料とサポート材が同一なため材料費を抑えられること、また造形速度が速いため3Dプリンタの中では高い生産性が高い点がバインダージェット方式のメリットです。
一方で、材料に結合剤が含まれていることから高い強度の実現が難しく、強度を高めるためには材料に応じて含侵処理や焼結処理を施す必要があります。また、造形材の影響により、微細な加工が難しい点もバインダージェット方式のデメリットとなります。
パウダーベッド方式
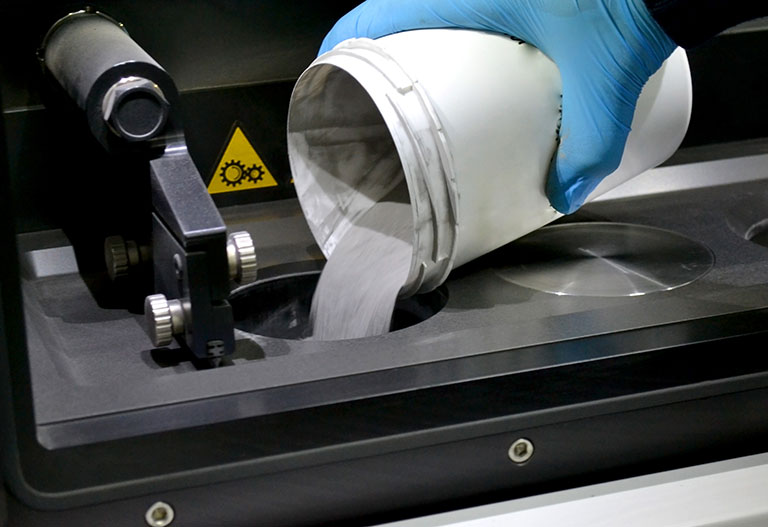
粉末床溶融結合法ともよばれるパウダーベッド方式では、造形材料を敷き詰めたプールの中で造形したい部分にレーザービームや電子ビームを照射し、造形材を一層ずつ焼結することで狙いの形状を実現します。
バインダージェットと同様に造形の材料とサポート材が同一である点に加え、焼結することで高い強度を実現することが可能です。また、高い精度の造形を実現できることもパウダーベッド方式のメリットといえます。
しかし造形物の表面が滑らかにならない点、また造形速度が高くない点はパウダーベッド方式のデメリットです。滑らかな形状を実現するためには、切削加工などの後処理が必要となります。
加えて、粉末材料には粉塵爆発は粉塵の吸引など、材料の管理には注意が必要なため、管理ルールを設定しておくなどの対策が必要です。
指向性エネルギー堆積方式
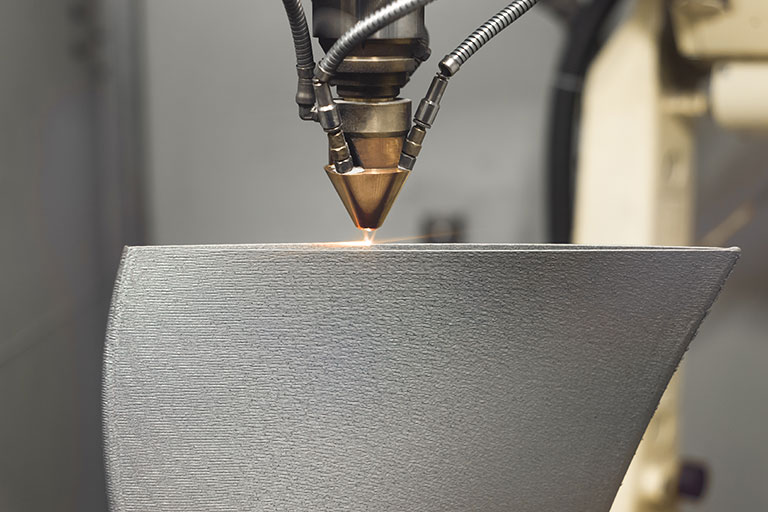
指向性エネルギー堆積方式は、レーザーメタルデポジションともよばれる造形方式で、粉末やフィラメントに加工された材料を排出し、レーザーなどの熱源によって加熱・溶融・積層する造形方式です。
複数種類の材料を混ぜて使用できるためさまざまな特性を実現でき、造形が速いため生産性が高い点が特徴です。また、原理的には大型化が容易なため、導入する設備が対応できていれば大型の製品も造形できる点がメリットといえます。
さらに、レーザーや電子ビームなどは融点が高い材料でも溶融できるため、他の造形方式では対応が難しい、融点が高い金属にも適用できる点は、指向性エネルギー堆積方式の大きなメリットです。
一方で、熱源設備の導入にコストが必要な点、使用する金属の特徴次第では精度の高い加工が難しい点などがデメリットとなります。高い精度が必要な場合には、パウダーベッド方式と同様に切削加工などの後加工が必要です。
シート積層方式
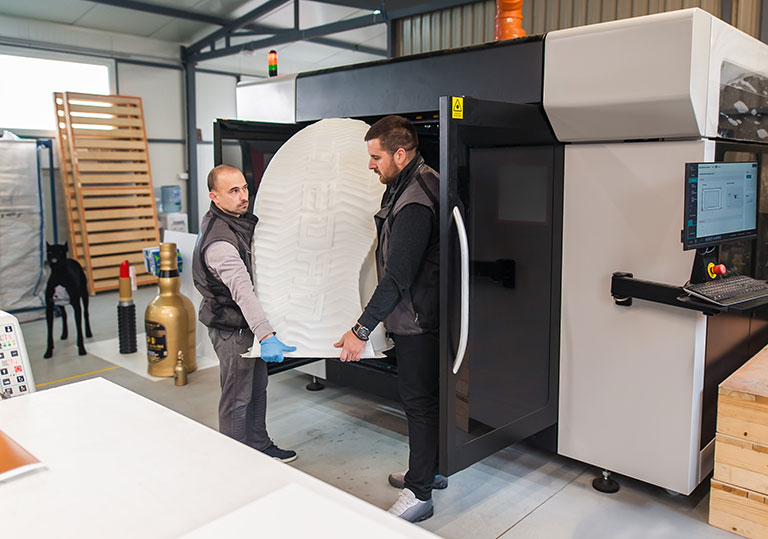
シート積層方式は、樹脂や金属、紙などのシート状に加工した材料を断面に沿って切断しながら積層する造形方式で、ラミネート積層法ともよばれます。
シート状であればさまざまな材料に対応できる点、硬化の際に熱源や光源、化学反応などが不要なため、簡素な設備構成で実現できる点がメリットです。その結果、設備導入コストやランニングコストも、他の造形方式と比較して安価に抑えられます。
一方で、それほど造形精度が高くない点、3Dプリンターの大きなメリットのひとつである中空形状などの複雑な形状が実現できない点がデメリットとなります。また、造形物に不要なサポート部分の除去も必要になるため、材料ロスが生じる点もデメリットです。
光造形方式の用途拡大
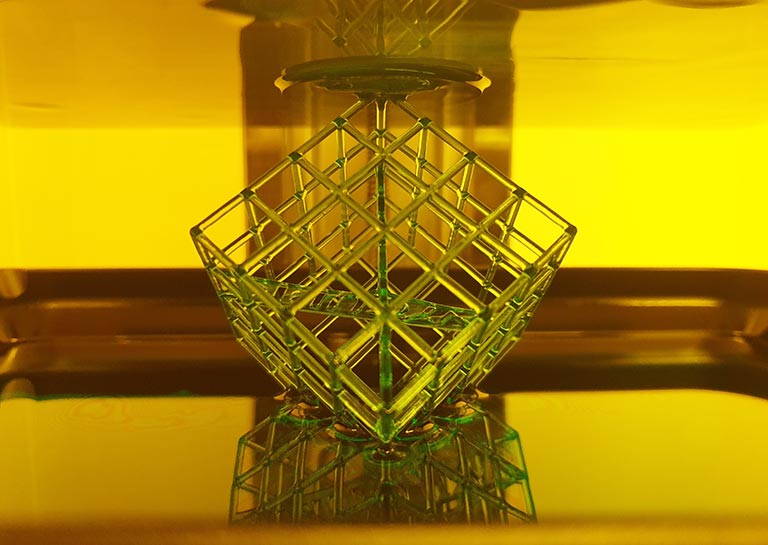
3Dプリンタは他の加工法と比較して新しい技術であり、産業用途の需要拡大から新たな技術開発が続けられています。
例えば、光造形方式は設備開発によって微細な加工を実現できるようになっており、電子部品製造や医療機器製造、また新たな技術開発を進める研究機関などにも導入されています。
3Dプリンタの造形方式を比較し導入を検討する場合には、新たに開発されている設備や造形方式の情報を取得して、導入目的に合致した造形方式・設備を選択することが重要です。
BMFにおける光造形方式のアプリケーション
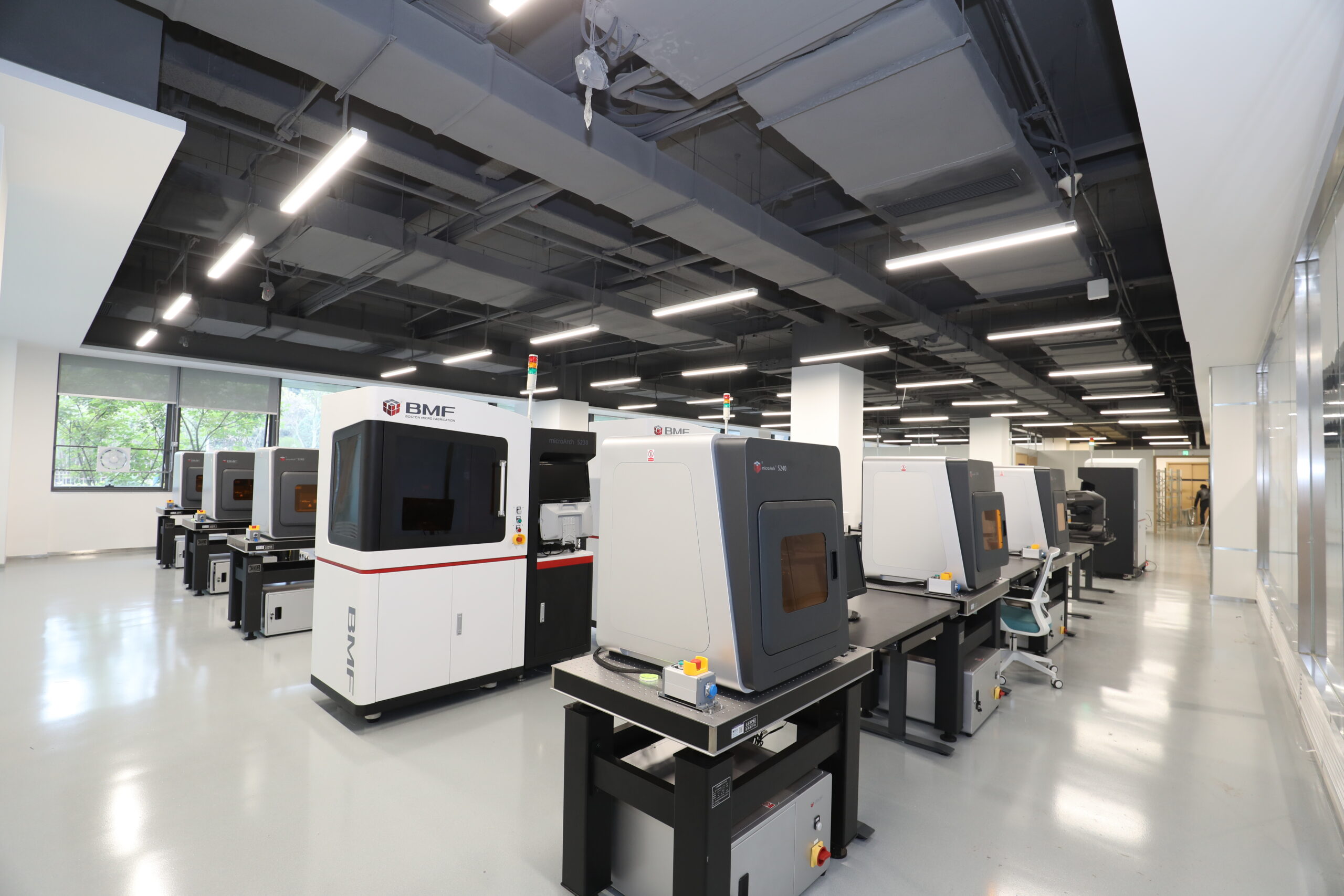
BMFでは、光造形方式の用途が拡大するなか、PµSL(Projection Micro-Stereolithography)と呼ばれる、独自の光造形技術を開発。PµSL技術は、高い精度が求められる産業用途のニーズに応えています。
BMFの超高解像度3Dプリンタによる、アプリケーションをご紹介します。
電子部品
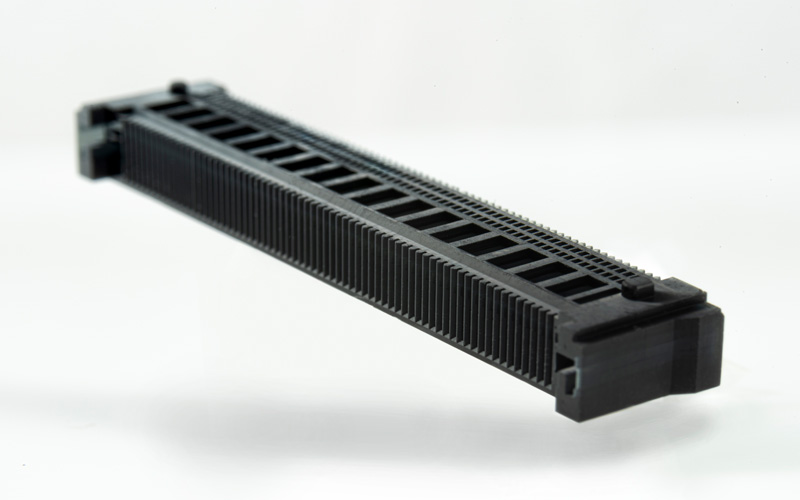
PµSL技術は、大手電機部品メーカーのコネクタや、ソケットなどの精密部品の試作開発で採用されています。
コネクタベースの試作
電子機器に欠かせないコネクタベースです。
最小穴径0.1mm・最小壁厚0.1mmの精密な試作部品を、1日以下の納期で成形することができます。
半導体チップアレイソケットの試作
マイクロプロセッサと回路基板を接続するためのソケット部品です。
切削加工では難しい1500個ものマイクロホールを、一体成形することができます。
半導体ランドグリッドアレイの試作
半導体実装で使われるパッケージ部品です。
射出成形では難しい階段構造が含まれた2500個もの台形穴を、一体成形することができます。
医療業界
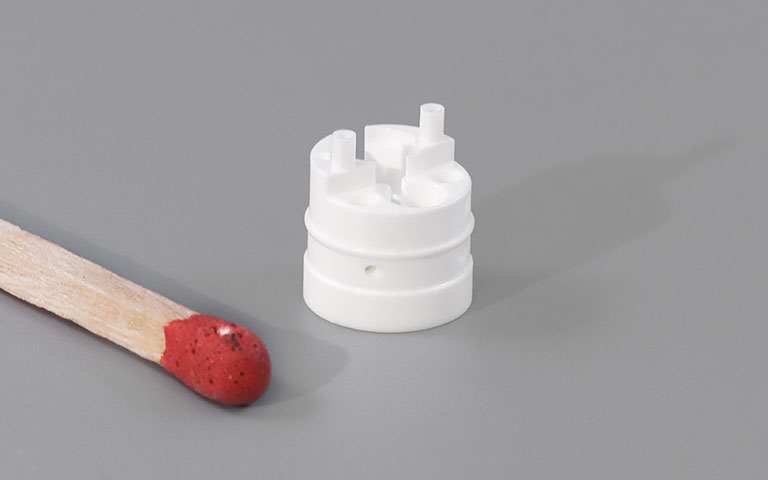
PµSL技術を使用して、体内に埋め込むステントや医療チューブ、内視鏡ハウジング、遺伝子シーケンサーバルブプレートなど、医療部品の試作開発が進んでいます。
内視鏡ハウジング部品
内視鏡カメラをカバーするための精密部品です。
超精密3Dプリンタによって、複雑な構造体を結合なしで一度に造形することができ、小型化によって、患者の痛みや不快感を軽減しました。
心臓血管ステント
血管などの管状部分を内部から拡げ、血流や血圧を改善する医療器具です。
超精密3Dプリンタによって、従来の金属材料から、生体適合材料を使ったステントへの置き換えが実現しました。
シリンジニードル
樹脂製の使い捨て注射針です。
超精密3Dプリンタによって、複雑な注射針の一体造形が実現しました。手術に合わせた、注射針のカスタム造形も可能です。
研究機関

PµSL技術は、バイオニクス、マイクロ流体デバイス、マイクロロボット、マイクロシステムなど、さまざまな分野の基礎研究に利用されています。
遺伝子シーケンサーバルブプレート
DNAシーケンス解析などに使われる、バルブプレートです。
生体材料(バイオマテリアル)を使い、最小パイプ径0.2mmの三次元構造を造形することができます。
血液冷却レギュレーター
血液冷却によって体温を下げるために使われる、医療用のレギュレーターです。
耐高温材料を使い、正弦波形状の複雑なパイプを一体成型で造形することができます。
流体コネクタ
各種の流体実験や創薬に使われる、マイクロ流体チップです。
生体材料(バイオマテリアル)を使い、内部空洞が含まれる複雑な形状を組立不要で造形することができます。
オルガノイドモデル
オルガノイドは、新薬開発やバイオバンク、癌の精密診療、再生医療などに使われる3次構造の培養細胞です。
超高解像度3Dプリンタで細胞培養チップを造形することで、より大きく複雑な臓器組織を生成することができます。
3Dプリンタの基礎知識、造形方式による違いまとめ
3Dプリンタの中には、今回紹介したようにさまざまな造形方式があり、それぞれ特徴が異なります。まずはどのような造形方式があり、それぞれどのような特徴があるのかを把握することが重要です。
また、3Dプリンタの技術開発は現在も活発に行われており、新たな造形方式や設備の開発が進められています。常に最新の情報を取得することで、目的に合致した3Dプリンタの導入や活用につながるでしょう。