製造業では、製品開発期間の短縮や開発コストの低減が求められており、3Dプリンタの導入を検討する企業が増えています。3Dプリンタにはさまざまなメリットがありますが、デメリットもあるため、導入の際には双方を把握したうえで検討することが重要です。
この記事では、製造業において3Dプリンタを導入するメリット・デメリットを紹介します。
ミクロンオーダーの光造形3Dプリンターは、ぜひ一度BMFまでご相談ください
3Dプリンタとは
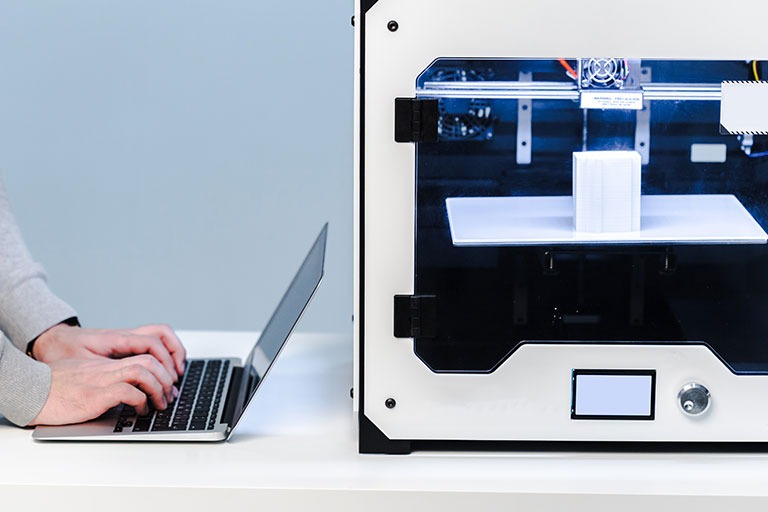
3Dプリンタを用いた製造方法は、アディティブ・マニュファクチャリング(AM)ともよばれます。あらかじめ設計した3Dモデルをもとに、材料を層状に積み重ねて物体を造形する製造方法、及びその製造を行う製造装置を意味します。
3Dプリンタでは、単一の材料だけではなく異なる材料を使用して精密な造形が可能です。また一般的な加工法では難しい、複雑な形状・デザインの一体成形や、フルカラーの造形にも対応しています。
3Dプリンタには、光造形方式やFDM方式、バインダージェット方式などさまざまな造形方式があり、それぞれ適用できる材料や造形物の特徴が異なります。また、造形方式によって必要な設備も異なるため、目的に応じた造形方式や設備の採用が必要です。
3Dプリンタ導入のメリット
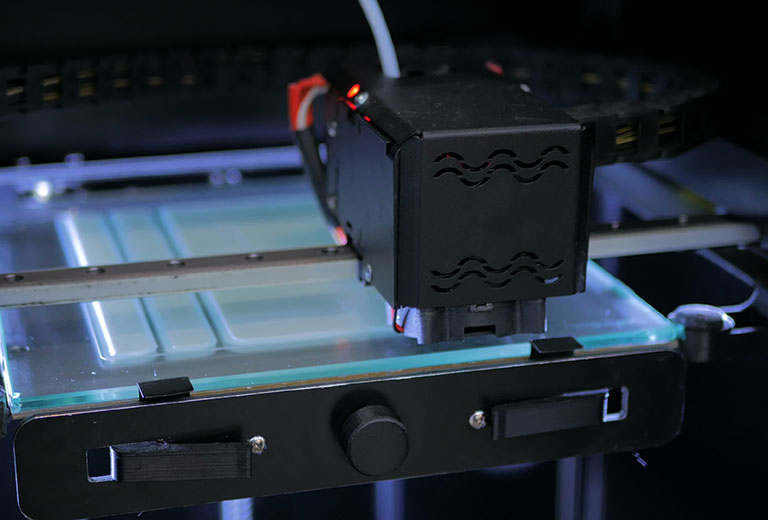
3Dプリンタを導入することで、以下のようにさまざまなメリットが得られます。
3Dプリンタ以外の加工法で解決できない課題がある場合には、3Dプリンタの導入が解決策となる可能性があります。
試作・開発期間の短縮
3Dプリンタの導入によって、試作期間・開発期間の短縮が期待できます。
新製品の開発を行う際には、試作品を用いて耐久試験や強度試験、性能試験などの評価を行う必要があります。しかし、試作品の準備には数日から数週間の期間が必要です。また、外注業者との加工前の調整に時間がかかると、さらに長期化してしまいます。
射出成形のように金型が必要な試作品製造を行う場合には数か月が必要となることもあり、気軽に試作を行うことができません。試作に時間がかかると、改良品の評価を行うのにも時間がかかるため、開発期間の長期化につながります。
切削加工サービスの中には、標準品から一定の変更の範囲内で最短即日加工できるようなサービスもありますが、実現できる形状や材料に制約があります。一方で、3Dプリンタを導入した場合、3Dモデルと材料を準備さえできれば、短期間での試作が可能です。
3Dプリンタの導入により試作期間を短縮することができれば、試作品を用いた試験の結果を速やかに試作改良品に反映させて再試験を行うことができるため、開発期間の短縮を実現できます。
複雑な形状の実現
3Dプリンタは、造形できる形状の自由度が高く、複雑な形状を実現できます。
切削加工や射出成形には、それぞれ実現できる形状の制約があります。例えば、切削加工では工具が干渉してしまうような中空形状は実現できません。また、射出成形で複雑な形状を実現しようとすると、成形不良を起こしてしまうリスクがあります。
このように、切削加工や射出成形で実現が難しい形状であっても、一層ずつ積層しながら造形を行う3Dプリンタであれば、一体成形することが可能です。複雑な形状を実現できれば、製品強度や精度の向上にも繋がるため、製品性能・品質の向上が期待できます。
在庫の低減
3Dプリンターを導入することで、試作品や材料の在庫を低減することが可能です。
急な追加評価などで試作品が必要になることもあり、すぐに評価に着手できるように在庫を保有しておくことが一般的です。しかし、使わないかもしれない在庫を準備し保管しておくことは、製品開発コストの増加につながるため望ましくありません。
3Dプリンターを導入していれば、試作品が必要になった際にすぐに試作品を準備できますので、在庫の確保は不要です。また、試作品の在庫を在庫の状態で確保しておくことで汎用性が高まります。
開発コストの低減
3Dプリンターを活用することで、開発に必要なさまざまなコストの低減が可能です。
自社で試作品の製造を行う体制構築が難しい場合には、外注を行います。3Dプリンターを導入し、社内で試作品の造形を行う体制を構築できれば、試作品の外注に関する費用の削減が可能です。
試作品の外注費用低減は単に製造費用だけではなく、製造に向けた外注先との打ち合わせ時間や出張時に移動に関するコストも不要となります。
3Dプリンターは導入コストやランニングコストが必要となりますが、試作品製造の機会が多い場合には十分回収が可能です。
3Dプリンタ導入のデメリット
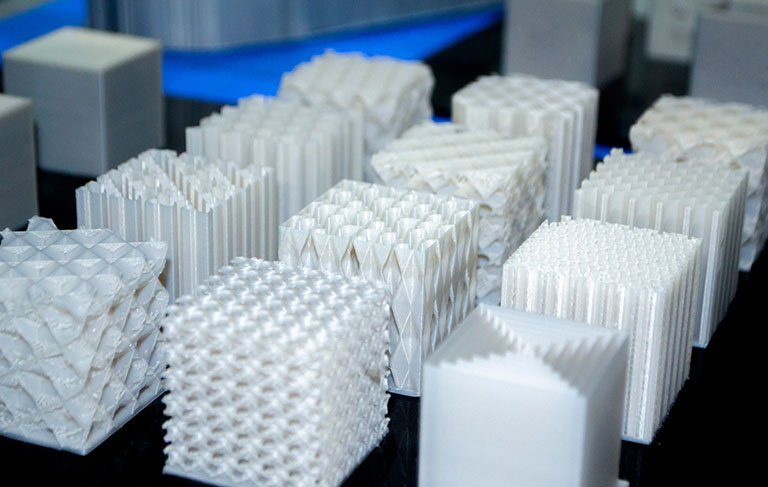
3Dプリンタの導入には、ここまで紹介したようにさまざまなメリットがあります。
一方で、3Dプリンタの導入時にはデメリットもあるため、あらかじめデメリットを把握したうえで対策をしておくことが望ましいです。
大量生産に向いていない
3Dプリンタは、射出成形などの大量生産に向いている加工法と比較して加工に時間がかかるため、大量生産には向いていません。また、材料のコストが高くなることも、大量生産向けの加工法ではない理由のひとつです。
一方で、複数の製品を同時に造形できる3Dプリンタの造形方式もあり、造形速度の向上に関する技術開発も進められています。どの程度の生産数量、生産速度が必要なのか、目的に合致しているかどうかを確認して加工法を選択することが重要です。
適用できる材料が限られている
3Dプリンタにはさまざまな造形方式があり、造形方式に応じて適用できる材料が異なります。例えば、材料を加熱する造形方式では熱可塑性樹脂、紫外線などの光を照射して硬化する造形方式では光硬化性樹脂の採用が必要不可欠です。
新たな造形方式・3Dプリンタ本体の開発によって3Dプリンタを用いた加工法に適用できる材料は増えています。材料の物性と造形方式の特徴から、狙いの製品を自社で導入する3Dプリンタで造形できるかどうかは、事前に確認する必要があります。
強度・耐久性が十分でない場合がある
3Dプリンタによる造形品は、目的によっては必要な強度や耐久性が確保できない可能性があります。3Dプリンタは、造形する際に一層ずつ積層造形を行うことから、各層の上下の結合部分が弱く、強度が不足する場合があります。
また、樹脂を用いた3Dプリンタでの加工では光硬化性樹脂を使用する場合があり、光硬化性樹脂は耐候性が低いため、屋外や直射日光を受ける場所で使用する場合には注意が必要です。
3Dプリンタで製造された製品でも、強度の高い材料の選定や造形後に熱処理を行うことで高い強度を実現できる場合もあります。必要な強度や耐久性を明確にしたうえで、それを実現できる材料・造形方式の選択が重要です。
切削加工と比較して精度が不十分な場合がある
高い寸法精度が必要な製品の加工法として、切削加工が代表的です。
3Dプリンタはさまざまな形状を実現できますが、切削加工と比較して実現できる精度が十分でない場合があります。高い寸法精度が必要な場合には、3Dプリンタでの造形後に切削加工を行うことで、狙いの精度を実現できます。
従来の3Dプリンタの課題を払拭する、BMFの3Dプリンタ
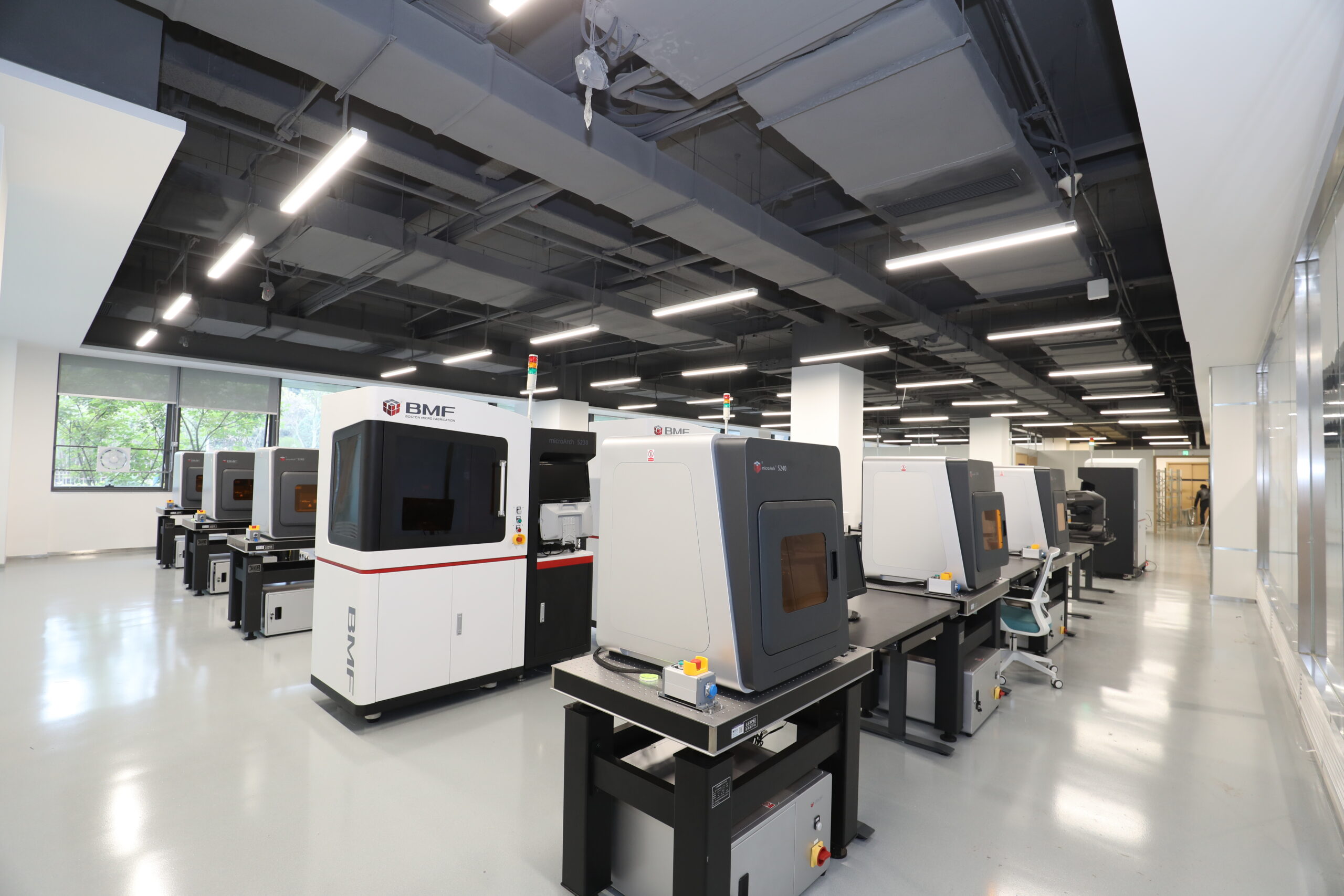
BMFではPµSL(Projection Micro-Stereolithography)と呼ばれる、独自の光造形技術を開発。ミクロンオーダーの造形精度で、高い精度が求められる産業用途のニーズに応えています。
またBMFでは、PDMSキャスティングや射出成形用のモールド印刷に適した「可溶性犠牲樹脂」を開発。可溶性犠牲樹脂は、硬化後に熱アルカリで溶解することができ、切削加工や射出成形が苦手とする複雑な形状の造形について、さらに精密で高速な造形を可能にします。
可溶性犠牲樹脂によるアプリケーションをご紹介します。
PDMSデバイス
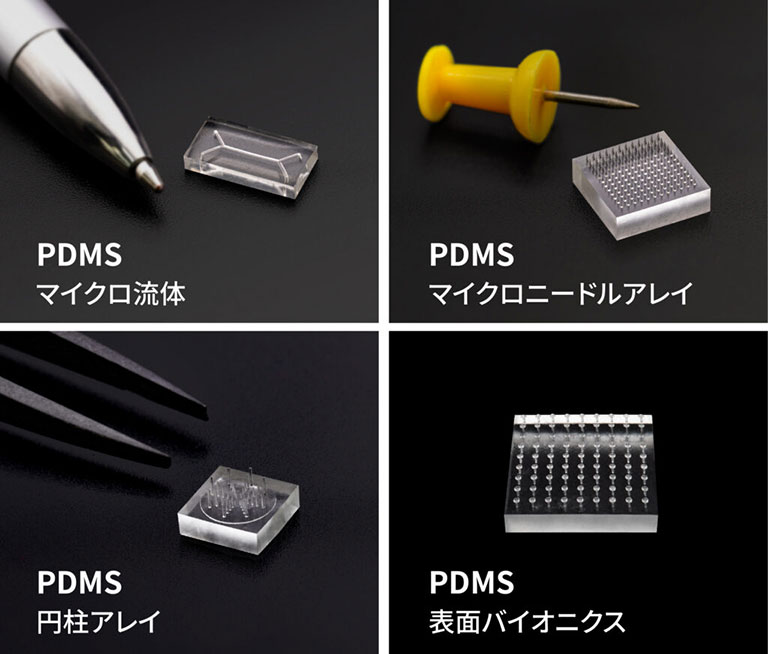
PDMSはさまざまな生物学的製薬関連製品や、科学研究用デバイスに広く使用される材料です。3Dプリンタのデメリットにひとつに、切削加工と比較して精度が不十分なことが上げられますが、可溶性犠牲樹脂で印刷したマスターモールドでPDMSを成形し、その後マスターモールドを熱アルカリで溶解することで、精密で複雑な三次元微細構造を持つPDMSデバイスを簡単に製作することができます。
射出成形用のモールド印刷
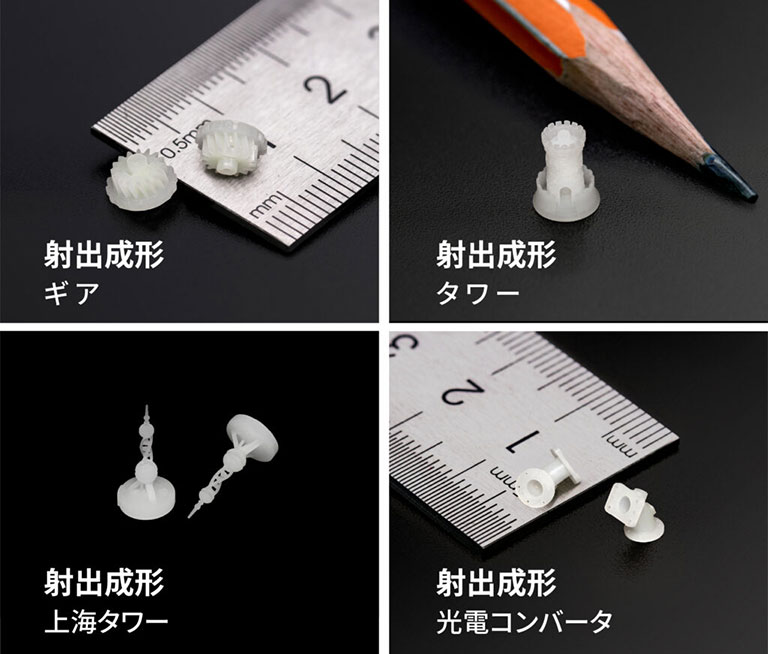
3Dプリンタのデメリットにひとつに、適用できる材料が限られてしまうことが上げられますが、可溶性犠牲樹脂で射出成形用のモールドを印刷してから、一般的なエンジニアリングプラスチック(POMなど)を使い射出成形を行うことで、さまざまな材料に対応することができます。
3Dプリンタの導入メリット・デメリットまとめ
3Dプリンタを導入することで、従来は実現できなかった複雑な形状の実現に加えて、開発期間の短縮や開発コストの低減につながります。一方で、3Dプリンタの導入には適用可能な材料の制約や強度などのデメリットがあるため、注意が必要です。
3Dプリンタの導入によるメリット・デメリットを事前に把握しておくことで、自社の目的にあった3Dプリンタの選定が可能になるため、これらの情報を把握しておくことが重要です。