製品の高性能化や小型化を実現するためには、ミクロンオーダーの精密加工が求められます。例えば、自動車の心臓部であるエンジンやトランスミッション、半導体部品、航空機の部品にもミクロンオーダーの精密加工が必要です。
この記事では、ミクロンオーダーの加工を実現する加工方法と、3Dプリンタで精密加工を行うメリット、3Dプリンタによる精密加工のアプリケーションについて紹介します。
ミクロンオーダーの光造形3Dプリンターは、ぜひ一度BMFまでご相談ください
ミクロンオーダーの精密加工方法
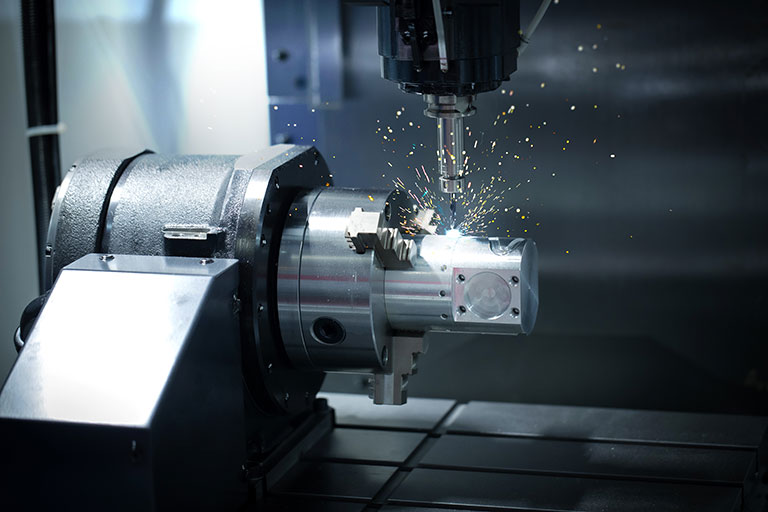
ミクロンオーダーの精密加工とは、マイクロメートル単位(1/1000mm)で行う加工です。ミクロンオーダーの精密加工を実現できる加工方法にはどのようなものがあるか、代表的な加工方法を紹介します。
切削加工・研削加工
切れ味がよく耐久性の高い工具を使用すれば、切削加工や研削加工でミクロンオーダーの精密加工が実現できます。すべての加工を切削で行ったり、他の加工の仕上げを研削で行う場合もあります。
切削加工は、3次元の形状を実現できますが、バリや切粉が生じてしまう点がデメリットです。また加工中に変形してしまうような「変形しやすい材料」「硬度が高すぎる材料」の場合には、ミクロンオーダーの加工に対応できない可能性があります。
レーザー加工
レーザー加工はワークに直接接触しないため、ワークの変形を最低限に抑えることができ、高精度な加工に最適です。レーザー加工は切断だけでなく、文字や図形のマーキングにも活用されています。また加工ワークは金属だけでなく、ゴムや樹脂、木材などにも対応しています。
レーザー光は種類によって出力やパルス幅が異なるため、用途・目的に応じて近紫外線レーザー、遠紫外線レーザー、超短波パルスレーザーなどのさまざまなレーザーを使い分ける必要があります。
放電加工
アーク放電による熱でワークを溶解させる放電加工でも、ミクロンオーダーの精密加工が可能です。放電は加工液に浸された状態で行われるため、加工時にワークが発熱せず、熱による変形が起きにくい点が特徴です。
放電加工は、切削では加工が難しい硬度の高い材料も加工できますが、電気を通さないプラスチックなどの材料は加工できません。また、放電痕によって加工面が粗くなることがあるため、研磨などの仕上げ加工が必要になります。
プラズマ加工
プラズマを用いて加工ワークを切断するプラズマ加工でも、ミクロンオーダーの精密加工が可能です。導電性のある材料であれば加工でき、加工速度が速いことや、複雑な形状に対応できる点がメリットといえます。
一方で、通電できない材料は加工できないこと、切断以外の加工には用いられないことから、さまざまな要望に応えられるわけではありません。
3Dプリンタによるミクロンオーダー加工のメリット
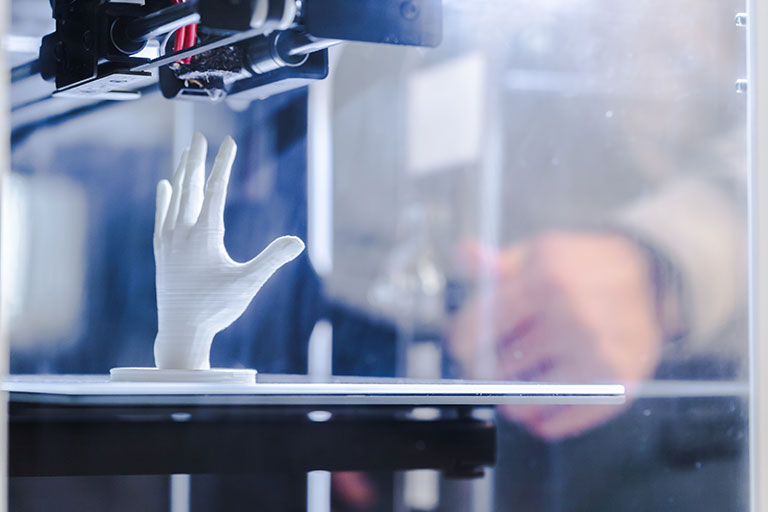
近年、樹脂や金属の加工方法として注目を集めている3Dプリンタでも、ミクロンオーダーの加工に対応した「高精度3Dプリンタ」が登場しています。
BMFでも、独自の光造形技術「PµSL」によって、ミクロンオーダーの加工が実現する「超高解像度3Dプリンタ」を製造しています。
3Dプリンタを用いた精密加工のメリットを紹介します。
複雑な形状の一体成型ができる
切削加工・研削加工の場合、工具がアプローチできない複雑な形状は実現できません。3Dプリンタであれば、複雑な形状の一体成型でも、材料を積層させて造形を行うことが可能です。
例えば切削加工の場合、中空構造の中空部分を加工することは困難ですが、高精度な3Dプリンタを活用すれば、中空構造だけでなく、微細な穴や微細な突起を持つ形状も造形できます。
また3Dプリンタで微細成形を行うことで、組み立てが不要になり、組み立てに伴う強度や品質の低下を防ぐことも可能です。
軟質素材や硬質素材の加工ができる
切削加工で軟質素材の精密加工を行う場合、加工時の圧力によって材料が変形してしまうため、高い精度を実現できません。また硬質素材の場合には、特殊な刃具を用いるか、それでも加工できない場合があります。
3Dプリンタであれば、機種・造形方式ごとに対応している材料であれば、材料の硬度に関わらずミクロンオーダーの精密加工を行うことが可能です。
材料のムダが少ない
切削加工や放電加工の場合、加工時に加工ワークを削り取ることで、材料のムダが発生してしまいます。材料のムダが生じると、その分が製品コストに反映されるため、試作コストの増加にもつながります。
一方で3Dプリンタであれば、切削加工のように材料を削り取るのではなく、材料を積み重ねることで狙いの形状を実現できます。3Dプリンタはコストを低減でき、環境面でも大きなメリットがあります。
試作コストが削減できる
3Dプリンタは、3Dプリンタ本体と材料、3Dモデルがあれば試作を行うことが可能です。形状を確認しながら繰り返し試作を行えるため、他の加工法に比べて試作コストを削減することが可能性です。
また3Dプリンタは金型を準備しなくてもよいため、射出成形後に追加工する場合と比較すると、数か月単位での開発期間短縮や開発工数の削減に大きく貢献します。
BMFにおける精密加工のアプリケーション
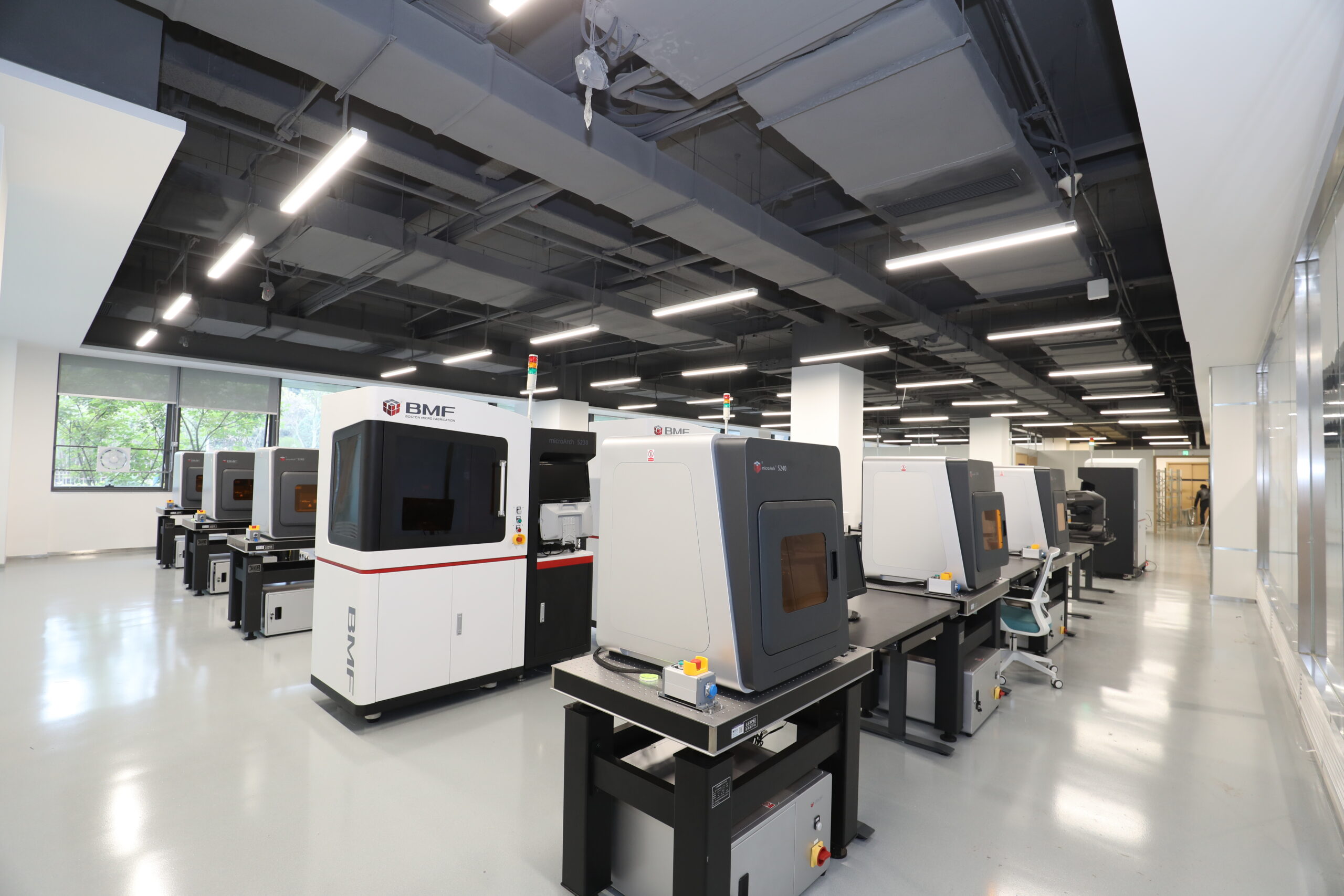
BMFの超高解像度3Dプリンタによる、精密加工のアプリケーションをご紹介します。
オルガノイドモデル
オルガノイドとは、新薬開発やバイオバンク、癌の精密診療、再生医療などに使われる3次構造の培養細胞です。従来のオルガノイドモデルは、体積が限られており、完全な臓器組織を生成することができませんでした。
超高解像度3Dプリンタで細胞培養チップを造形することで、より大きく複雑な臓器組織を生成することができます。
緑内障ドレナージ装置
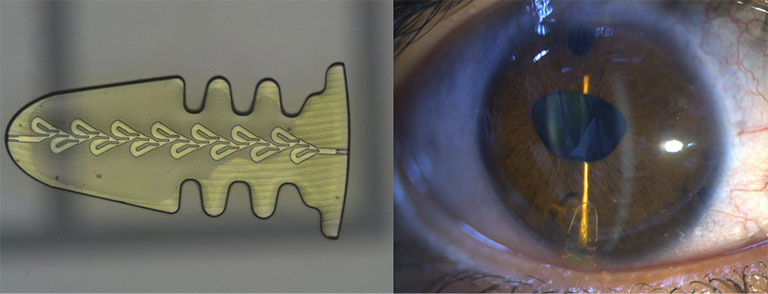
ドレナージ装置は、ドレーンを挿入することで、体内に溜まった液体を体外へ排出する装置です。
BMFでは、北京同仁病院(中国)と提携し、経角膜経路一方向性房水ドレナージ装置を共同開発。超高解像度3Dプリンタでレナージを造形することで、房水の逆流を防止するテスラバルブ構造を備えた、ドレナージ装置を実現しました。手術期の眼圧制御が優れており、緑内障の治療に成果を上げています。
医療部品
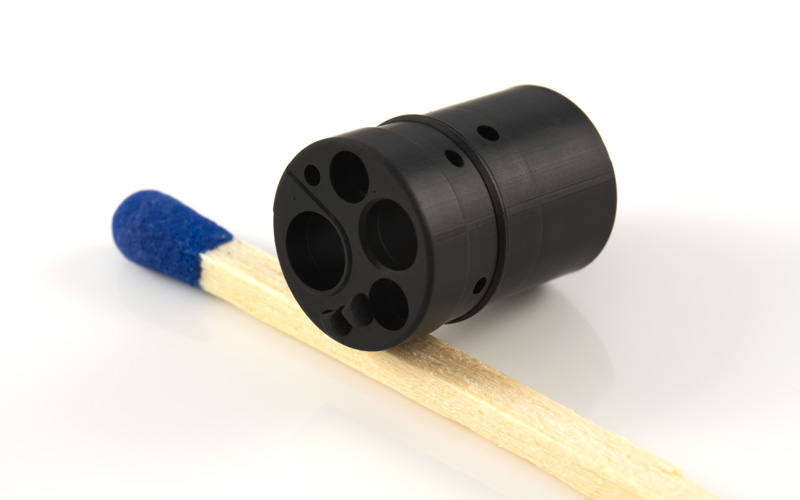
医療部品においては、高い精度が求められる内視鏡部品をはじめ、人体に埋め込まれる生体適合材料を使ったステントや、複雑な注射針の一体造形など、少量生産の3Dプリントに実績があります。
電子部品
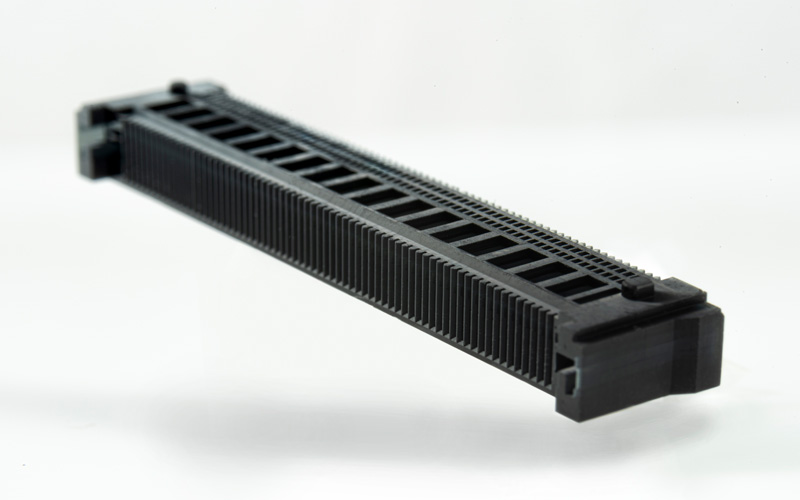
電子部品においては、最小穴径0.1mm・最小壁厚0.1mmのコネクタベースや、1500個ものマイクロホールを持った半導体チップアレイソケットなど、従来切削や射出成形では難しかったミクロンオーダーの3Dプリントが実用化されています。
ミクロンオーダーの精密加工法と3Dプリンタまとめ
製品の小型化・高性能化を実現するためには、ミクロンオーダーの精密加工が必要不可欠です。切削や放電加工・レーザー加工などで、精密加工を実現できる場合もありますが、中には実現が難しい複雑な形状や加工対象の材料もあります。
近年、高精度3Dプリンタが登場したことで、これまでミクロンオーダーの精密加工が難しかった材料の加工も実現できるようになっています。今後も、3Dプリンタによる加工技術が進歩するとともに、さまざまな材料・形状の加工が実現するようになるでしょう。