製品の電子化・IoT化が進むにつれて、電子基板同士を接続するコネクタの需要が高まっています。コネクタは汎用性が高いものだけではありません。製品ごとに、独自の要求仕様を必要とするものも多くあります。
これまでコネクタを試作するためには、金型を製作する方法が一般的でした。しかし近年は、3Dプリンタの活用が増えています。
この記事では、コネクタ試作における3Dプリンタの活用例を紹介します。
ミクロンオーダーの光造形3Dプリンターは、ぜひ一度BMFまでご相談ください
電子部品に使われるコネクタとは
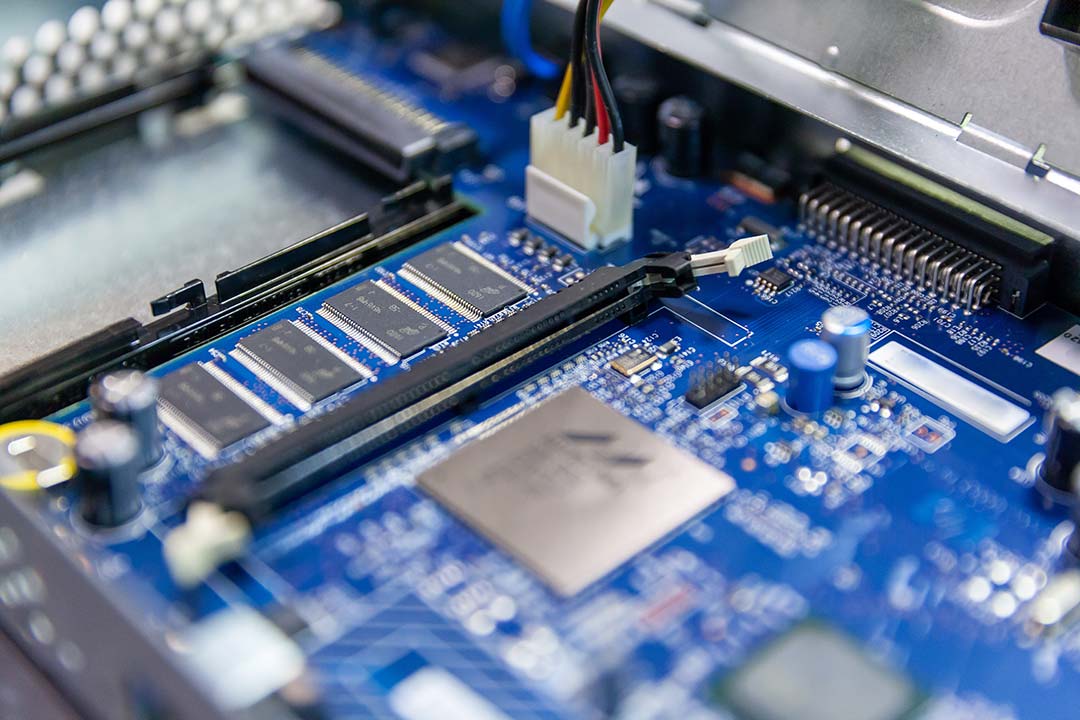
電子部品は信号の送受信や給電のため、外部との接続が不可欠です。その際に用いられるのが「コネクタ」です。近年はBluetoothなどの無線接続が一般的になってきましたが、テレビやオーディオプレーヤーなど、日常生活でコネクタを利用する機会も多くあります。
コネクタの用途は、製品同士を接続するだけではありません。製品内部で使用されている電子基板同士を接続するためにも多く用いられています。例えば、自動車には1台あたり30~50個程度の電子制御ユニット(ECU)が搭載されており、それぞれのECUを接続・切断するために多くのコネクタが用いられています。
コネクタ開発のトレンド
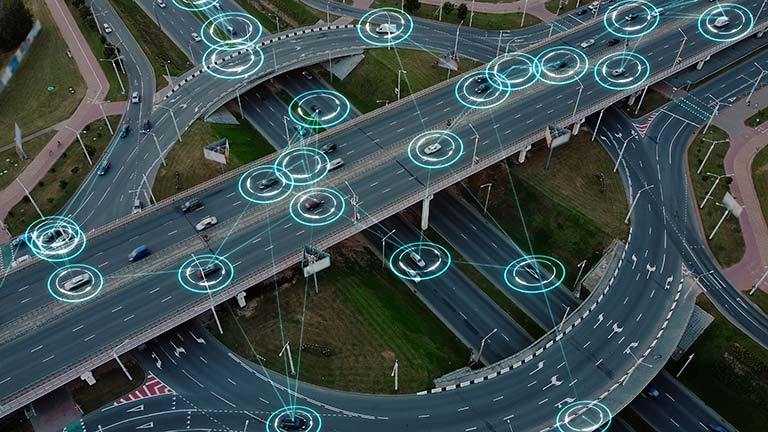
近年、コネクタの需要が高まっていますが、その背景にはさまざまな要素が複合的に関係しています。
例えば自動車業界では、以下のそれぞれの頭文字を取った「CASE」という言葉が用いられています。これらの実現には、車載用コネクタが必要不可欠です。
- Connect
- Automated
- Shared
- Electric
また、さまざまな製品をネットワークに接続できるようにするIoT化の推進や新たな通信規格である5Gの普及、これらに対応した製品の需要増加に伴い、コネクタの需要は年々増加し続けています。
一方でコネクタに求められる要求性能も高まっています。例えば、高速伝送が可能で、車載しても振動に耐えられること、他にも、小型化や耐熱性が高いことなどがあげられ、用途が増えるとともに新たな要求が生まれています。
コネクタの種類と用途
コネクタには、さまざまな種類があります。ここでは、製品内部で用いられる内部接続用のコネクタに絞って、代表的なものを解説します。
基板対基板コネクタ
基板対基板コネクタはもっとも代表的なコネクタで、ボードツーボード(BtoB)コネクタともよばれます。プリント基板とプリント基板、もしくはプリント基板とFPC(Flexible Printed Circuit)を接続する際に用いられる基板です。
幅広い製品に採用されるためさまざまな性能を要求され、その種類も多岐にわたります。例えば、高い接続信頼性や振動を吸収するフローティング構造の採用などがあげられます。
FPC/FFC用コネクタ
FPCは薄い絶縁シートに電気導体で回路を印刷したもので、柔軟性が高い点が特徴です。またFFC(Flexible Flat Cable)は、薄い矩形の導体を絶縁シートで一定間隔ごとにラミネートしたものです。
FPC/FFCコネクタはFPCとFFCを接続するためのコネクタで、基板対基板コネクタと比べて薄い点が特徴的です。
カードエッジコネクタ
カードエッジコネクタも、製品の内部で基板と基板とを接続するために用いられるコネクタです。メモリーカードなどのカードを差し込むメス型のコネクタで、低コストでありながら抵抗が少なく信頼性の高い接続を実現できます。
主に、プリンターなどのOA機器やノートPC、車載機器などに多く用いられており、標準規格が制定されているため汎用性が高い点も特徴です。
シールドコネクタ
ノイズ対策として、ケーブルの配線部分を保護するための金属のシェルを配置したコネクタを、シールドコネクタとよびます。金属でできたシールドが付属しているシールドケーブルと共に用いることで、ノイズをグランドに流すことが可能です。
電線対電線/基板コネクタ
その名の通り、電線と電線および電線と基板を接続するタイプのコネクタを、電線対電線/基板コネクタとよびます。
製品ごとに独自設計となる場合が多く、特にモバイル機器などの小型端末向け、車載向けの分岐コネクタなど、多種多様な対応が必要です。
コネクタ試作における課題とは
コネクタが多種多様な製品に使用され、需要が高まるにつれて、製品の開発段階におけるコネクタ試作にはさまざまな課題が生じています。ここでは、代表的な課題を紹介します。
開発リードタイム
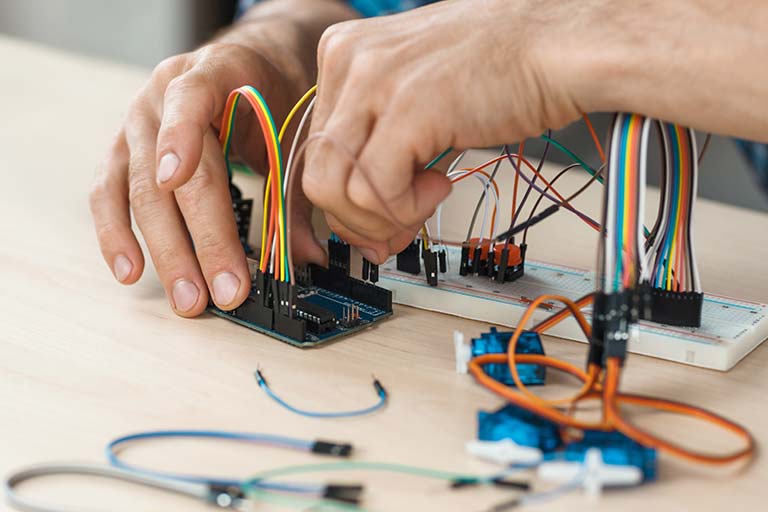
コネクタの設計は机上で進めますが、手で接続するコネクタであれば、作業性に問題がないか試作品を製作して確認します。また、狙い通りに嵌合できるか、接続部を壊すことなく外すことができるかなどの確認も必要です。
コネクタの試作では、金型を起こすために一ヶ月程度の時間がかかってしまいます。製品設計をしてから確認までの間に一ヶ月以上の時間がかかってしまっては、開発リードタイムが長く、開発サイクルが短いコネクタの試作には対応できません。
微細な形状・高精度の実現
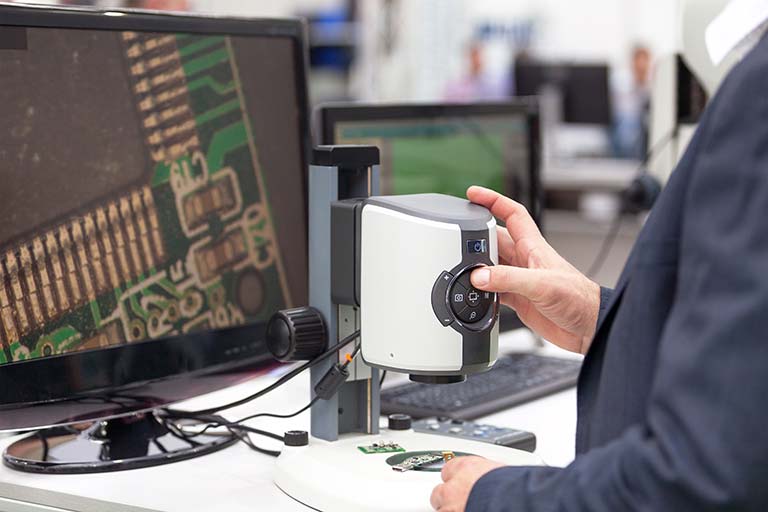
コネクタの中には、微細な形状のものもあります。性能確認を行う試作品にも高い精度が求められますが、微細なコネクタを高精度で試作するのは簡単ではありません。
試作の精度が低い場合、量産後に設計課題が見つかることもあります。その結果、再設計・試作・評価・型の製作に必要な期間が増え、開発期間の長期化にもつながります。
3Dプリンタを活用したコネクタの試作について
近年、3Dプリンタでコネクタ試作を行う企業が増加。BMFの超高解像度3Dプリンタであれば、独自の光造形技術「PµSL」によって、微細形状のコネクタに試作が実現。コネクタ製造の国内最大手、世界トップクラスの実績を誇るヒロセ電機様でも、コネクタの試作造形に、BMFの3Dプリンターが採用されています。
ここでは主に、試作金型を使用する場合と比較した3Dプリンタ活用のメリットを紹介します。
開発リードタイムの短縮
コネクタ用の試作金型を起こすためには、約一ヶ月程度の期間が必要です。また使い勝手やノイズの影響など、試作しなければ分からない要素も多く、一度の試作で最終品の設計が完了すると限りません。複数回の試作が必要になれば、その分試作期間も延びてしまいます。
3Dプリンタによる試作であれば、金型の設計期間や製作期間を削減できるため、試作リードタイムを大幅に短縮することができます。
試作コストの低減
試作金型は高価なため、コネクタの試作コストも高額になってしまいます。開発リードタイムと同様に、複数回の試作を行うためには、予算の確保が課題となります。
3Dプリンタを試作に活用すれば、金型の開発や製造コストは不要です。試作期間が短縮されれば、人件費も削減できるため、試作コストの大幅な低減につながります。
BMFのコネクタアプリケーション
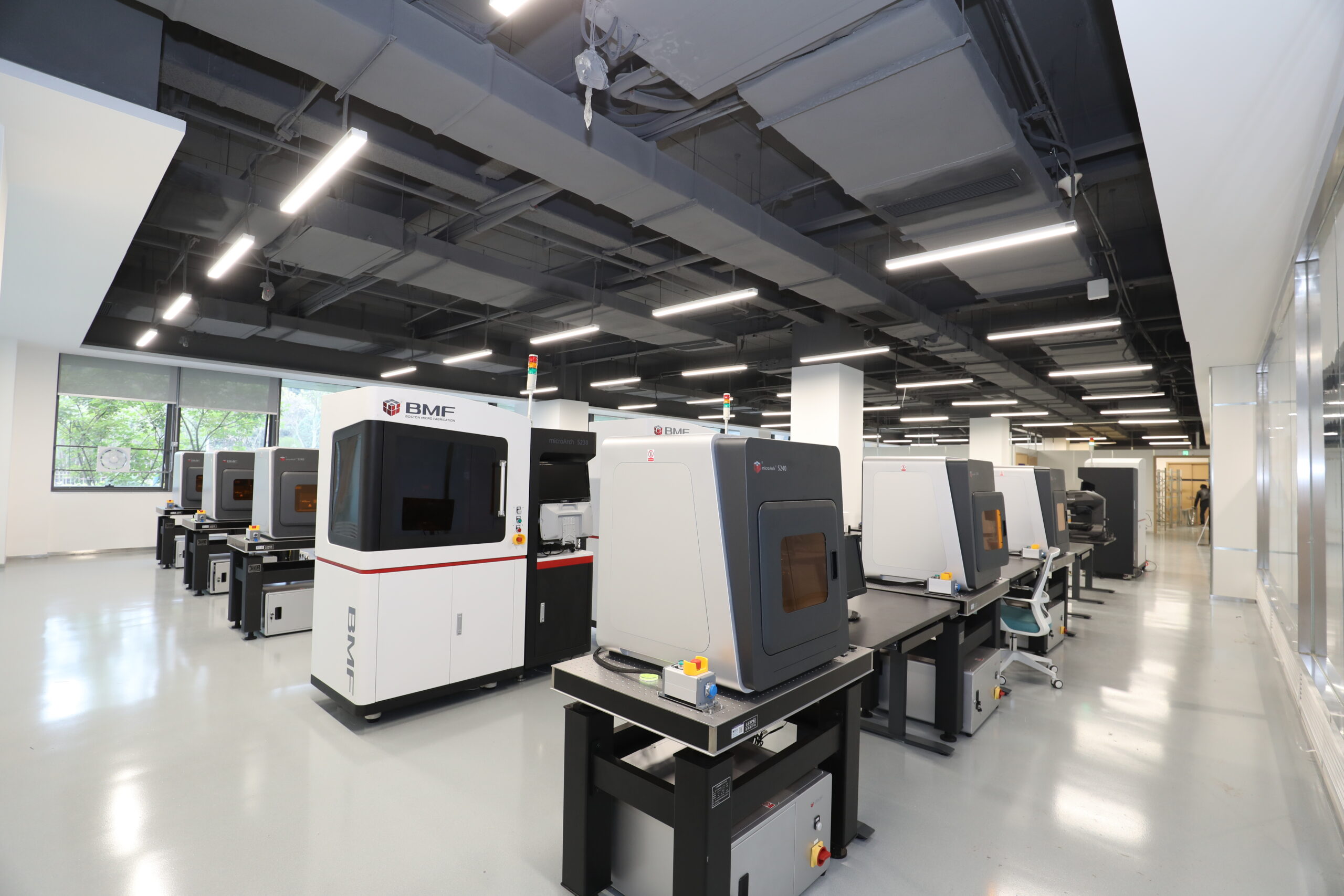
BMFの超高解像度3Dプリンタによる、コネクタの製作事例をご紹介します。
RJコネクタ
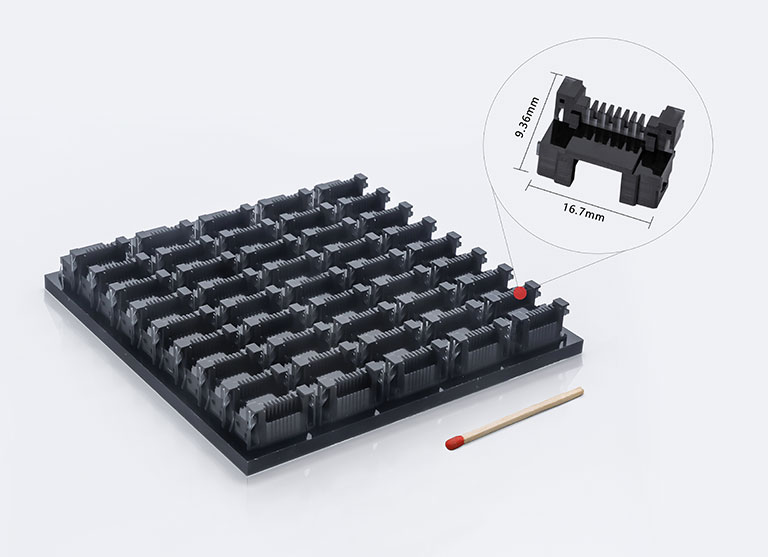
LANコネクタなどに使われる通信用コネクタの試作例です。
外形サイズは16.7×9.55×9.36mmで、最小壁厚0.14mmの微細な試作が可能です。
また試作だけではなく、多数個取りの小ロット生産にも対応することができます。
(使用機種:microArch® S240)
ソケット
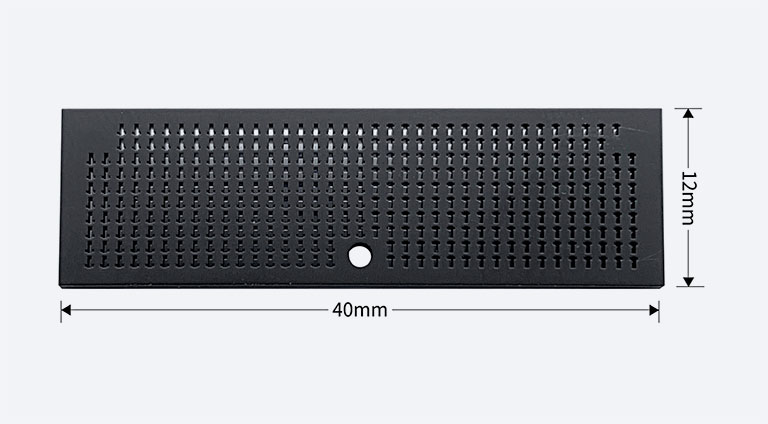
基板内部に使われるソケットの試作例です。
外形サイズは40×12×3.5mmで、最小孔径0.07mmの微細な試作が可能です。
(使用機種:microArch® S240)
cLGAコネクター
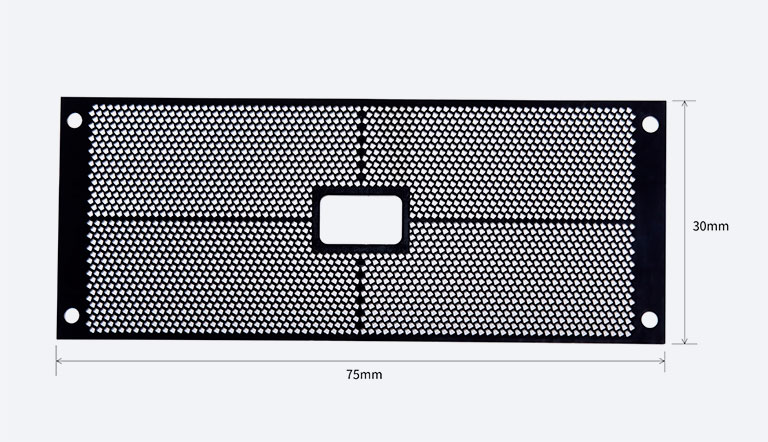
基板間を接続するLGAソケット用コネクタの試作例です。
細かい階段構造が含まれた、1700個以上もの台形孔の微細加工が可能です。
(使用機種:microArch® S140)
コネクターベース
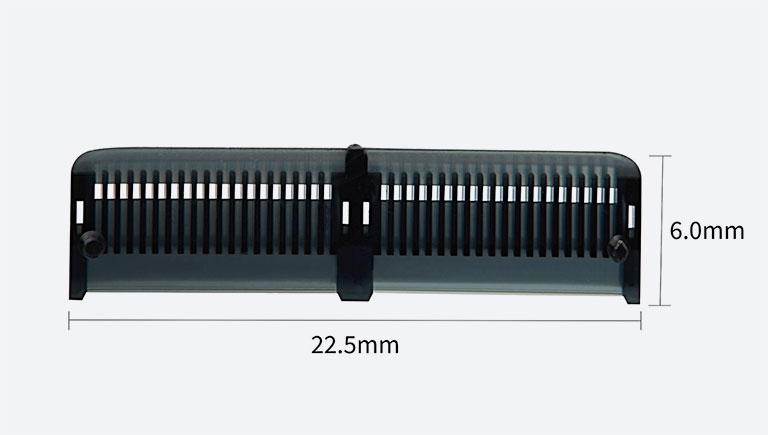
コネクタの接続に使われる、ベース部品の試作例です。
外形サイズは22.5×4.0×6.0mmで、最小孔径0.1mmの微細な試作が可能です。
(使用機種:microArch® S240)
コネクタ試作に役立つ3Dプリンタの活用まとめ
コネクタは、要求がさまざまで開発サイクルも短いことから、短納期・低コスト・高精度の試作を行う必要があります。
3Dプリンタであれば、金型を使った試作と比較し、開発リードタイムやコストの面で大きなメリットがあります。5GやIoTが普及し、コネクタに求められる要求が増えるにつれて、コネクタ試作における3Dプリンタの導入も広がっていくでしょう。